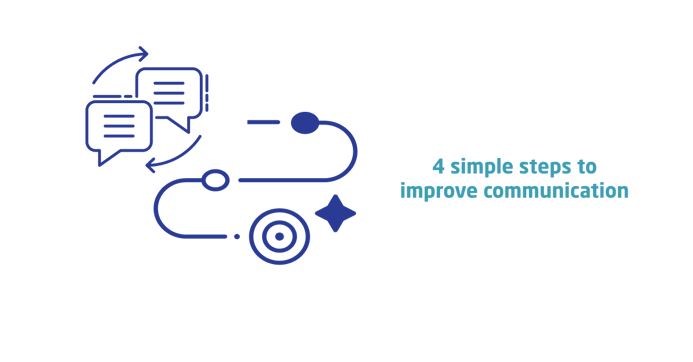
The key to improving communication between departments is really quite simple: mutual understanding and alignment.
It sounds obvious. But in practice, it can be challenging.
If you’re in maintenance or production or finance then you’re involved in asset management. And because asset management is everyone’s business, it means everyone must be involved and working toward common goals. The ISO 55001 Requirements state that the what, when, how, and who of communication must be determined. It’s easy to see though that it can often be a struggle to understand other departments, so here are 4 simple steps your organization can take to make the magic happen.
- Share goals.
- Build relationships.
- Form cross-functional teams.
- Use communication tools.
But first, a quick word on rivalry.
You probably work in a department. You probably experience rivalry with another department, right? On a regular basis? Even inter-departmental conflict? Increasingly tense rounds of email tennis. Dirty looks over the water cooler. Whispers and sneers in the hallway. Throwing the other department ‘under the bus’ at the weekly meeting. This is not uncommon at all according to one study. You could probably argue it’s human nature. You put people in ‘teams’ and they naturally want to outcompete the others – the rivals – even when working for the same company.
It's a hard thing to eliminate, rivalry. But ultimately, it wastes time and dollars.
But what is the problem between maintenance, production, and finance? If you work in process or manufacturing industries, you’ve probably heard these said:
Finance: Why does the maintenance manager have to buy the most expensive mechanical seals? There are plenty of cheaper ones available? Don’t they get profit and loss?
Maintenance: It’s ridiculous. We plan and schedule the maintenance down day, then production goes and cancels it. Again! They didn’t say anything in the meeting yesterday.
Production: Why does finance insist on buying cheap packaging from abroad? It screws up the wrapper machine every other day. They don’t get the pressure we’re under. Have maintenance got anyone capable of fixing it?
Sound familiar?
This is why senior organizational management must foster positive departmental relationships around shared and common goals. Get the people communicating and put them in cross-functional teams at every opportunity.
Let’s take a look at the four simple but critical steps to better communication, understanding, and alignment between maintenance, production, and finance.
1. Share goals
It is critical to conquer differences and achieve success. This starts with finding common ground, and a good place to start is finding common goals. In the context of asset management, all departments’ goals should be derived from the overall organizational plan:
So, what this means is that although departments will have their own goals, objectives, and tasks, everything should be derived from the organizational plan, i.e. the shared set of goals that everyone has a ‘line of sight' of. This creates the desired alignment.
One example of a maintenance objective that traditionally ‘affects’ production is planned downtime to perform preventive maintenance (PM). This is often a misalignment and the cause of friction between the two. Production is under pressure to hit the numbers. And if it is behind, then it sees PMs as something that can be deferred for another time. Maintenance sees PMs as essential to maintaining asset performance, i.e. to hit the numbers. Maintenance and Production must agree on and stick to the plan and it must be derived from the Organizational Plan.
2. Build relationships
To take this step is to get people talking and quite often this means informally. People need to get to know each other. What good is it if the production team and the maintenance team are located in different buildings and rarely see each other? And if the finance team operates 100% remotely? Here are some ideas your organization could implement:
Team lunches: Get the pizzas and soft drinks ordered once in a while. It can help to promote an informal chat. Maybe schedule it after a project close-out or maintenance shutdown period.
Create clubs/teams: How about creating a company soccer or basketball team? There are so many options to bring different people together.
Quarterly retreats: Team building events for group problem solving or simply getaways for the senior team leaders of maintenance, production, and finance. These come with a cost but will deliver long-term stronger relationships and goal achievement. And that’s a stronger bottom line.
3. Form cross-functional teams
The best time to do this is on an asset management project. For example, the introduction or upgrade of a new process line. This is a great example of when teams need to be formed from different departments: production, maintenance, finance, projects, procurement, health and safety, and others. But the point is that it must be run and managed as a professional project. Here are the critical steps to forming a successful cross-functional team:
- Identify the expertise required for a successful outcome. It’s no good having the 1st year apprentice responsible for developing the maintenance plan.
- Select the right personalities – you need team players. Leaders, worker bees, and everything in between. Not a team full of egos.
- Ensure quality leadership - the project will be a learning curve for all, but ensure you have experienced project leaders driving it.
- Be clear on each team member's purpose. Confusion costs.
- Create a team charter: consensus and agreement on objectives. Remember, ‘the line of sight’?
- Set a specific budget.
- Create project schedules and plans and ensure everyone has visibility at all times.
- Create lines of communication and a communication plan.
4. Use communication tools
Whether on a project or not, what are the tools that we can use to bring maintenance, production, and finance together to communicate effectively? Lucky for you, there are plenty:
Intranet & forums – An open repository of information where finance could upload business financial performance; production could show targets and compliance, and maintenance could demonstrate KPIs for work management and availability. Forums are particularly good for knowledge transfer between departments.
Digital newsletters – These replace the old paper copies. Delivered by email, it is a great way to quickly convey information to all departments in an organization. Great for presenting case studies: production introducing new recyclable packaging; maintenance upgrading to a new EAM or CMMS; finance securing funding for a new process line.
Digital signage –. These signs are programmable and can show all sorts of department updates and are a great alternative to newsletters for those who don’t work at a computer: technicians and operators for example.
Collaboration tools – There are many out there such as Google Meet and Docs, Teams, and so on. These tools allow departments and teams to collaborate in real-time by file sharing, app sharing, using video and voice calls, and even instant messaging. A great place to share cross-departmental information.
EAM/ CMMS – Rather than be integrated and the issues that follow that, these functions can be built-in into an ERP system. This allows for a single source of information for finance and maintenance. Greater awareness of costs is achieved due to the software not being siloed from the ERP, and the synchronization between the two allows for increased productivity and easier communication. On top of all this, analytics and KPIs are easily communicated to all – whether that be asset availability, open work orders or MTBF.
So, these are four simple steps to help improve communication between maintenance, production, and finance and, in fact, any department in your organization in the context of asset management. Communication - like culture - can make or break organizations.
As someone once said, ‘teamwork makes the dream work’.