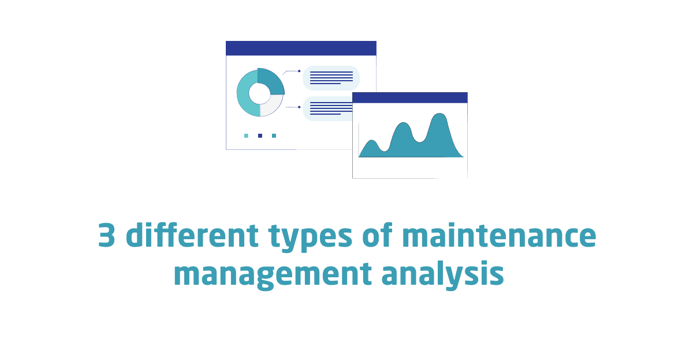
If there’s anything more important to maintenance management than collecting data, it’s knowing how to use it effectively.
Here, we’ll guide you through the relationship between maintenance and analysis, the various methods at your disposal, and what you can do to optimize the process.
The role of analysis in maintenance operations
If maintenance and data are like peanut butter and jelly, analysis would be the bread that ties them together.
In other words, data without analysis is essentially a set of numbers without meaning. They don’t help you optimize your maintenance activity or reduce unplanned downtime. Simply put, maintenance management analysis is what brings data to life in an actionable, mission-oriented way.
That’s why analysis is a critical component of any effective maintenance management program. It ensures reliability for your most critical assets, puts a cap on maintenance costs, and provides you with a set of repeatable, data-driven workflows that trigger a cascading wave of productivity throughout the organization.
3 types of analysis every maintenance department should know
Just as there are many types of strategies – preventive maintenance, corrective maintenance and the several that fall within either of these categories – there are also many ways to analyze your data.
Although each method differs slightly in their approach, all aim to achieve the same overarching goals: Protecting your critical assets from unplanned downtime and maximizing the efficiency of your maintenance operations. Knowing which to use for any given maintenance task boils down to understanding the basics:
1. Root cause analysis (RCA):
This method takes a systematic approach to identify the origin of an incident, such as an unexpected asset failure. There are many ways to perform a root cause analysis, but generally speaking, the process consists of describing what, why and how something happened and the actions maintenance personnel can take to prevent it from happening again.
For this reason, RCA can be understood as part corrective action, part preventive maintenance. Even though it happens after the fact, RCA aims to mitigate equipment failure down the road.
2. Reliability centered maintenance (RCM):
Reliability centered maintenance analysis is a structured framework for analyzing the functions and failures of any given piece of equipment. Rather than focus on preserving the asset over time, this method is concerned with preserving its core capabilities (i.e. ensuring its functions can be reliably performed).
In simple terms, RCM determines what maintenance personnel should do to detect, eliminate or reduce the frequency or severity of asset failure.
3. Failure mode and effect analysis (FMEA):
Failure mode and effect analysis systematically identify potential failures and the impact of their outcomes. FMEA differs from other methods because it takes a predictive approach to maintenance activity rather than corrective action.
In turn, FMEA allows your maintenance team to quantify the consequences of asset failure and strategically limit their impact on business continuity.
Of course, these processes depend on having accurate data. Unsure if your facility is collecting the right information? These are a few key indicators you’ll need to consider:
- Unplanned downtime.
- Maintenance costs.
- Mean time between failure.
- Work order cycle time.
A streamlined approach to analyzing maintenance operations
It should be noted that maintenance management analysis is no easy task – especially if you’re not using the right tools. The truth is that you likely have too much information to sort through by hand.
But with an enterprise asset management (EAM) or computerized maintenance management software (CMMS), you can optimize data collection and analysis. Solutions like Dynaway’s Microsoft Dynamics 365-based platform collect data from work orders, sensors, and other ERP modules to help inform decision-making during the maintenance planning process.
The result? Streamlined maintenance, process efficiency, and maximum equipment uptime.