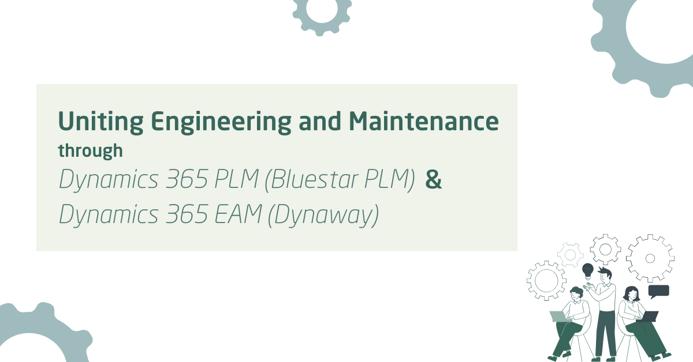
Integrating Bluestar PLM and Dynaway’s Enterprise Asset Management (EAM) within Microsoft Dynamics 365 Finance & Supply Chain Management (D365 F&SCM) creates a single, unified environment for product development, manufacturing, and maintenance.
In many organizations, engineering (product lifecycle management) and maintenance (asset management) traditionally operate in silos.
This separation often leads to data duplication, communication gaps, and inefficiencies – for example, engineers may release designs without insight into maintenance issues, while maintenance teams lack direct access to the latest design data or Bill of Materials (BOM).
By bringing Bluestar PLM and Dynaway’s asset management solutions, which are embedded solutions and natural extensions of Microsoft Asset Management module in D365, together, companies can eliminate these silos. In fact, this integrated solution bridges the gap between Engineering and Maintenance by connecting the entire enterprise on the same software platform. The result is end-to-end visibility from initial design to after-sales service, all within the familiar D365 interface.
Bridging Engineering and Maintenance: Why Integrate PLM and EAM in Dynamics 365?
To understand the value of this integration, consider the roles of each system.
Product Lifecycle Management (PLM), as provided by Bluestar PLM, manages the entire lifecycle of a product, from initial design and CAD models through engineering change orders (ECOs), production, and ultimately service.
Enterprise Asset Management (EAM), as provided by Dynaway’s solution, helps organizations manage and maintain their physical assets across different teams and locations in one integrated system.
Historically, PLM and EAM systems have operated separately. This can cause issues such as the engineering team not knowing which designs are causing frequent field failures, or maintenance not having the latest drawings or parts lists.
Integrating Dynamics 365 PLM and Dynamics 365 EAM addresses these pain points by ensuring:
Continuous Data Flow
Bluestar PLM embedded in D365 allows engineering data (items, BOMs, 3D models, drawings, etc.) to be shared seamlessly with other departments. Meanwhile, Dynaway’s EAM solutions, built into D365, are advancing the Microsoft Asset Management module and interfacing with other modules like inventory, procurement, and production.
When combined, it means that a change in the engineering BOM is automatically reflected in maintenance spare parts lists, and service data (like failure rates or maintenance feedback) is accessible to engineering, all through one system. This single source of truth ensures everyone is working off the same up-to-date information, reducing errors and miscommunications.
For example, if Bluestar PLM defines a machine consisting of 100 parts (with a structured BOM and sub-assemblies), once that machine is installed in the field, Dynaway can register it as an asset with the exact same breakdown. The maintenance team doesn’t have to manually enter what parts the machine has; they see the eBOM from Bluestar as the asset’s structure (which often mirrors a maintenance BOM). This complementary flow ensures accuracy and saves time. As Bluestar PLM is the source of product truth, Dynaway uses that truth to drive maintenance schedules and tasks.
End-to-end Lifecycle Visibility
An integrated PLM-EAM solution connects the dots from design to decommission. Thanks to this integrated system, when an engineering change is made, operations and maintenance are immediately aware of the new revision and its impact.
Conversely, if a quality or reliability issue is discovered during maintenance, engineering is alerted instantly to address it. This end-to-end visibility helps prevent scenarios where a product fault continues unchecked simply because information was trapped in a separate system. It also aids regulatory compliance and traceability, since all product history and service records are linked.
Efficiency and Collaboration
An integrated solution eliminates duplicate data entry and manual hand-offs between engineering and maintenance. Sales, engineering, purchasing, production, and service teams all collaborate on the same platform. Bluestar PLM inside D365 connects the entire enterprise and end-to-end business processes, from early product development all the way to product fabrication and service.
Maintenance planners can see upcoming design changes and prepare, while engineers can design with knowledge of maintenance needs (e.g., designing for easier servicing). The result is faster turnaround times – design changes get implemented without waiting for lengthy data transfers, and maintenance work orders are generated with the correct, updated parts and instructions.
Enhancing the Bluestar-Driven Process with Maintenance Insights
While Bluestar PLM excels at managing design and change processes up to the point of release, Dynaway enhances the process by adding maintenance-centric functionalities:
Preventive Maintenance Scheduling
Preventive maintenance can be significantly optimized using Dynaway’s Maintenance Strategy feature, which enables organizations to define time- or counter-based triggers to automatically generate maintenance plans based on engineering standards or manufacturer recommendations. When Bluestar provides asset-specific data like expected component lifespans, Dynaway uses this intelligence to schedule replacements proactively, mitigating risk, avoiding unscheduled downtime, and ensuring regulatory compliance.
To streamline technician execution, Dynaway extends preventive maintenance with Advanced Maintenance Checklists that provide clear, repeatable procedures. These include actions, reviews, tracking compliance or quality assurance, delivering consistency, and reducing the potential for skipped steps.
Work Order Management
When maintenance work orders are executed, Dynaway logs the details (which parts were replaced, what was repaired, who did it, how long it took). All this happens in the same system that Bluestar’s data lives in, meaning anyone with access to Dynamics 365 can trace these events.
For instance, a product engineer could look up a particular serial-numbered asset and see its full maintenance history to date. This kind of visibility is possible only because Dynaway feeds data into the Bluestar/ERP ecosystem rather than an isolated tool.
Spare Parts and Inventory Alignment
Bluestar PLM defines all the parts (and their revisions) that make up a product; Dynaway ensures that when those parts are needed for maintenance, the ERP’s inventory and procurement modules know exactly which part (and revision) is required.
For example, if engineering issues a change via Bluestar that introduces a new, more robust bearing (a new part number or new revision), Dynaway’s maintenance module will automatically reference the updated part for future work orders. This prevents scenarios like using an old spare on a new design (or vice versa). Bluestar manages the design changes, and Dynaway operationalizes those changes in the maintenance phase, ensuring the engineering intent is carried through to service. Maintenance and procurement can then coordinate to stock the correct new parts. Without such integration, maintenance teams might unknowingly use outdated components or miss critical updates, leading to errors.
Dynaway's Work Order Kitting functionality allows planners to automatically compile kits for scheduled jobs using approved spare parts. These kits can be aligned with inventory forecasts and reduce pick errors, delays, and excess stock. When Bluestar releases part revisions, Dynaway ensures work orders always reference the latest part specifications, eliminating the risk of using obsolete components. This ensures synchronization between design changes and operational execution.
Operational Feedback into PLM
Dynaway acts as both a consumer and a producer of data in the PLM environment. By capturing operational insights like asset failures, part replacements, and downtime causes, Dynaway feeds valuable performance data back into Bluestar PLM. This closes the product lifecycle loop, enabling engineers to initiate design improvements based on real-world maintenance feedback.
Failure Reports to Engineering
Dynaway logs critical work order execution details: parts replaced, work performed, technician assigned, and time spent - all within the same D365 ecosystem where Bluestar data resides. This system-wide visibility enables stakeholders like product engineers to view the entire maintenance history of a serialized asset.
Dynaway also enhances fault management via the Fault Designer, allowing technicians to systematically record component failures. These fault records can then feed into Dynaway’s analytics engine to identify failure trends and performance anomalies, helping inform engineering and procurement decisions.
Total Cost of Ownership and Lifecycle Data
Bluestar PLM can store all costs associated with a product’s development and production. By adding Dynaway, the costs (and efforts) in maintenance are also tracked. A company can analyze a product’s total lifecycle cost within one system - maybe a certain design is cheap to produce but very expensive to maintain over 5 years. Such insights would emerge when maintenance data (Dynaway) complements PLM data (Bluestar PLM). This helps decision-makers in product development to consider not just initial cost, but also serviceability and long-term costs; a true lifecycle perspective.
Why Dynaway is a Natural Fit (Complement) for Bluestar PLM Users
Bluestar PLM users have already embraced the idea of an ERP-embedded solution for engineering. Dynaway follows the exact same philosophy for maintenance.
Both embedded solutions in Dynamics 365 contribute to a consistent user experience as the integration is inherently smoother than third-party add-ons. Organizations don’t need to spend time building custom bridges between a PLM system and EAM, as the integration is out-of-the-box.
From a change management perspective, companies that have broken down the wall between engineering and manufacturing will find it logical and low-risk to also connect maintenance. It’s an incremental step in digital transformation: first connect engineering to ERP (design to manufacturing), then connect maintenance into the same thread (operations back to design). Each step yields greater visibility and efficiency. Dynaway’s maintenance solution amplifies Bluestar PLM benefits by ensuring the data loop doesn’t stop at product release but continues through service life.
Key Benefits of a Unified Engineering and Maintenance PLM–EAM Platform
Combining Microsoft Dynamics 365 embedded solutions - Bluestar PLM and Dynaway’s asset management delivers numerous benefits for both technical teams and business stakeholders. Below are some of the key advantages of this integrated approach:
Single Source of Truth
All stakeholders (engineering, manufacturing, procurement, maintenance, service) refer to the same data repository. Both Dynaway and Bluestar PLM contribute to this unified data model: Bluestar by managing the product and engineering data, and Dynaway by managing asset and maintenance data, all under the Dynamics umbrella.
Improved Efficiency & Fewer Errors
An integrated Dynaway + Bluestar + D365 environment reduces manual entry, ensuring accurate and current data across systems. Maintenance planners can auto-pull asset BOMs and design specs when scheduling tasks, guaranteeing precision in planning and execution.
If the organization uses Plant and Facilities Exposition (PFE), the EAM system can be configured to enable production-line operators to initiate work requests directly, speeding up response and minimizing downtime.
Enhanced Collaboration
By treating engineering and maintenance as two facets of a continuous lifecycle, collaboration improves. An engineering change committee can include a maintenance engineer’s input, since data on failure rates or maintainability is readily available. Similarly, maintenance teams can access 3D models or drawings from Bluestar PLM when working on complex equipment, improving the quality of repairs.
This breaking down of walls fosters a culture where engineers and maintenance technicians solve problems together rather than throwing issues “over the fence.” It echoes the idea that linking upstream and downstream processes yields real gains in efficiency, quality, and even innovation. Both Bluestar and Dynaway facilitate this linking of traditionally siloed departments.
Lifecycle Feedback Loop
Perhaps the most strategic benefit is the creation of a full digital thread from concept to disposal. Bluestar PLM covers the concept, design, and production phases, while Dynaway covers operation, maintenance, and service life. Together, they enable lifecycle insights. Companies can perform analyses such as reliability growth tracking, total cost of ownership calculations, or predictive maintenance triggered by design data. For example, knowing the exact revision of a part in a machine (thanks to PLM data in ERP) allows a maintenance system to suggest specific inspection points or replacement intervals (thanks to EAM data on failure patterns). Conversely, frequent maintenance issues can prompt a design review. This continuous improvement loop is only possible when PLM and EAM are tightly knit – something our combined solution achieves.
Circularity and Sustainable Maintenance
Bringing PLM and Asset Management data together is becoming more important due to trends like machine rebuilding, sustainability requirements, and the need for products to be repairable and adaptable. Having control over the design revisions allows companies to maintain and rebuild products later on.
Conclusion: A Unified Journey from Design to Service
Dynamics 365 PLM (Bluestar PLM) provides the foundation by integrating engineering with the core ERP. Dynamics 365 EAM (Dynaway) builds upon that foundation, ensuring that the asset’s operational life is also managed within the same integrated environment. For existing Bluestar PLM users, Dynaway is the logical next step to achieve a true end-to-end lifecycle management within Dynamics 365. It extends the value of your PLM investment into maintenance and reliability, without requiring a separate standalone system.
The Bluestar–Dynaway combination thus offers a comprehensive solution: Bluestar drives innovation and product data management, and Dynaway drives asset performance and maintenance excellence using that data. Together, they enable manufacturers to not only design and build better products but also keep those products running optimally through their lifespan.
This synergy leads to:
- - lower operational costs,
- - improved product quality (through feedback loops),
- - higher customer satisfaction.
It’s a classic case of the whole being greater than the sum of its parts – Bluestar and Dynaway's integrated solution creates a unified lifecycle platform that significantly enhances Industry 4.0 and digital thread initiatives for any organization.
For best practices on maintenance planning in Dynamics 365, check out the on-demand webinar: Demystifying Maintenance Plan, Strategies, and Schedules in Asset Management in D365 F&SCM. It provides practical insights into setting up preventive maintenance, strategies, and work order schedules in the Asset Management module. Also, for a broader view of how Dynamics 365 handles Asset Management (and how Dynaway’s add-ons extend its capabilities), visit our Asset Management Overview page. These resources will help you delve deeper into optimizing maintenance within a unified lifecycle platform – the perfect complement to your Bluestar PLM-driven processes.