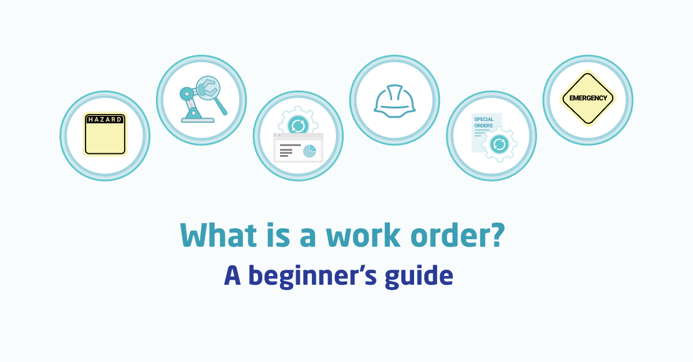
When you’re responsible for overseeing operations at one or more manufacturing or heavy industrial facilities, you surely have a great deal on your plate.
You want time for the most critical tasks and to strategize for long-term improvements when possible — but you have to balance those wants with the realities of your day-to-day workload.
Simply put, you’re being pulled in a lot of directions, but few of them are as central to your business as work order management. In situations where time is of the essence, work order software is a valuable asset. But the key to optimizing your work order process is knowing how to craft the ideal order and execute it as efficiently as possible.
In this guide, we’ll discuss the ins and outs of work order management and what you can do to streamline creation, distribution and evaluation.
What is a work order?
The work order process is a central component of the maintenance department. Without a work order, your maintenance team wouldn’t have the necessary context and information they need to perform their maintenance tasks to the best of their ability.
In facilities management, a work order is a formal document that communicates key information about how a maintenance request should be executed by the technician. A work order request can be sent from any unit of business with a need for repair or routine maintenance.
It’s easiest to think of a work order as the compass that guides the maintenance work to completion. Traditionally, facilities relied on pen and paper to complete the work order form, but now EAM systems are making work orders available in digital format for easy accessibility. Despite the vast cost-efficiencies that digital solutions provide – as evidenced by McKinsey – many businesses are still handwriting their work orders.
In either case, information critical to the work order include:
- Description of the maintenance task.
- Identification of the customer, department or individual who made the request.
- Estimated task completion date.
- Name of the technician or maintenance team responsible for the task.
- Location of the requested maintenance operation.
- Parts, tools and other prerequisites.
- Cost estimates.
Work order vs. Work request vs. Purchase order
It’s important to note that the term ‘work order’ shouldn’t be confused with ‘work request’ or ‘purchase order.’ Although often used interchangeably, the truth is that they’re very different pieces of the same puzzle.
To eliminate confusion, it’s best to understand each one individually. Here’s how they compare:
- Work requests: A work request – or, work order request – is a submission from staff, customers or other personnel that requests maintenance activity for an asset. Once a request is received by maintenance management staff, such as a planner or manager, they determine whether or not it should be approved.
- Work orders: Once the work order request is approved, a work order form for said request confirms the maintenance activities and sets them in motion. Notably, work orders may also be created based on scheduling and may not require a formal work request.
- Purchase orders: Whereas the work order assigns work to the maintenance technician, a purchase order authorizes the acquisition of essential goods and services from third-party vendors, such as spare parts and equipment. The purchase order provides information on what to buy, how much and when they should be delivered.
Types of work orders
No two work requests or corresponding work orders are the same. To set your maintenance work off on the right foot, you need a thorough understanding of each work order type:
- Inspection: This type of work request is sent when a given component, device, machine or system needs to be checked for any issues — typically combined with a pre-established schedule. Inspections may well uncover no problems at all, but they're critical for due diligence.
- Preventive maintenance: As with inspections, preventive maintenance work orders are not necessarily requested in response to any obvious problem with a machine, but rather to get out ahead of malfunctions or faults before they happen. This is in contrast to reactive maintenance, which only issues a maintenance work order after an asset failure.
- Safety: If a safety work order has been requested, it means that the business unit making this request wants the maintenance team to focus on updates and repairs that will specifically benefit the physical safety of workers using a given machine or system, as opposed to focusing on the equipment's life span.
- Hazard-specific: Maintenance work that involves specific (and particularly dangerous) hazards demands a specific work order. For example, if the repair demands skill and experience with faulty wiring, circuitry and other electrical components, an electrical work order would go out to maintenance management. Similarly, if hot work, line breaks, confined spaces or heavy machinery are involved, the work order must reflect that. (Additionally, a maintenance technician will have to request a permit to work that is just as specific.)
- Emergency: An emergency order would be requested when immediate maintenance is necessary for the sake of worker safety or equipment health. If the situation is serious and immediate enough, the work order process might be bypassed to get repair personnel on the job right away (at the discretion of the maintenance manager).
- Special order: This type of order covers anything that wouldn't fit under any of the previously mentioned categories: replacements of legacy assets, installation of new equipment to improve the overall maintenance situation and so on.
The ideal work order process
On a surface level, the internal work order workflow looks somewhat simple: A department within the business makes a work request to the maintenance department, which can either approve or deny it. If approved, the job will be scheduled, and then another more formal work order will be sent to the technician responsible for completing the task enumerated in the original request. That individual completes the necessary maintenance. Then, the work order is considered closed, and it is archived for future reference.
In reality, the work order process isn’t so open and shut. To truly optimize the workflow, it may be wise to think of work order management in a more focused and holistic way. Consider the following set of steps:
- Identify: Experienced production operators and technicians should identify the issue, and use exact language to detail it in work orders (e.g., "Forklift actuator failing to activate hydraulics and raise forks").
- Prioritize: Is this the most pressing corrective maintenance issue for the team to address, or should it be put on the back burner? Answer the question based on factors like asset criticality, production needs, safety requirements and quality.
- Plan: Maintenance managers must draw up detailed plans for team members handling complex jobs. In addition to instructions for necessary tasks, include any relevant safety requirements, especially those steps necessary for regulatory compliance.
- Schedule and assign: Find the ideal time for the maintenance to take place and assign a technician with relevant experience. Keep priorities in mind — assign the most skilled techs to the most difficult orders and leave routine maintenance to those with less experience.
- Execute: Complete the work in a timely manner (without sacrificing quality).
- Evaluate: Look at what went right or wrong with the order, what could've been done better or faster, the parts used and so on.
In facilities management, things rarely go off without a hitch – especially work orders. One small error in the process has the potential to send disruptive ripple effects throughout the rest of the workflow.
Following these best practices is the best way to avoid errors during the process:
- Use a template for work orders that includes fields for all appropriate information and is easy for techs to follow.
- Automate the process wherever possible.
- Maintain visibility throughout the process so you can quickly notice any issues and address them before they become bigger problems.
- Track orders using relevant metrics including mean time between failure, mean time to repair or replace, overall equipment effectiveness and cost.
Benefits of work order software
The work order life cycle can be difficult to manage with so many other critical tasks begging for your attention. Work order management software is an ideal solution that not only optimizes the work order process but also affords you the opportunity to focus on other operations.
By leveraging a digital work order management system rather than relying on paper-based methods, you stand to gain a number of advantages, the benefits of which include:
- Work order efficiency: Digitally crafted work order forms are typically completed faster than their physical counterparts. This is because they provide all necessary instructional materials and resources within the work order itself so that technicians can access them easily from any location using a mobile client.
- Centralized maintenance management: Digital solutions eliminate the need to juggle multiple systems. With a work order management system, you gain one source of truth that allows you to track every detail of your maintenance operations from start to finish.
- Less paperwork: Fewer papers to file means less physical storage space you need in your facility. But even more importantly, it means you can reduce the risk of human error when inputting information by hand.
- Real-time data: Work order software empowers you to turn data into actionable business intelligence, allowing you to make strategic improvements for long-term growth.
These advantages are just the tip of the iceberg. According to Deloitte, businesses with advanced use of digital tools are three times more likely to experience revenue growth and are twice as profitable.
You need not search long to find a la carte work order software solutions that can manage your maintenance operations. But it's unlikely that these tools or field service management (FSM) tools will offer enough functionality to be quite worth the expense.
You'll be best off if you use the work order management tools available in a computerized maintenance management system (CMMS) alongside a leading-edge EAM tool like Dynaway, which is neatly built into Microsoft Dynamics 365. Taking this approach not only streamlines the work order process for more efficient results – from initial request to order closure – but also fully integrates this function with all other facilities, inventory and asset management processes, allowing your organization to realize more comprehensive oversight.
To learn more about Dynaway’s features, contact us or take a look at our recent eBook.