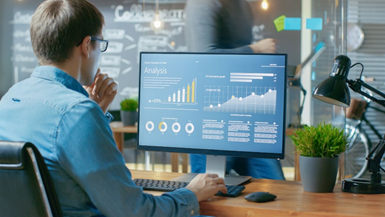
During the heat of a long and difficult maintenance shift, industrial engineers sometimes 'forget' to fill out the work order feedback for failures they have fixed.
They've spent the last 5 hours on their backs underneath a dark and oily conveyor that failed catastrophically on the night shift. Can you blame them for not wanting to type out paragraphs of text?
This is a shame.
Why?
Failure reporting is crucial
Failure reporting data and information is like gold dust to reliability and maintenance managers. It is precious. Inputted consistently, a few simple words can lead to great insights, analytics, and leverage for business performance improvement. It'll help you reduce unplanned downtime and avoid future failure incidents.
So, why not make it easier for your engineers?
You need a 21st century CMMS
Just to rewind a little for a moment, think of those organizations that don't use a CMMS for work management. Pen and paper and whiteboards are the order of the day. They may even have a shift handover book. Done that way, your organization has no hope of failure reporting leading to reliability improvement.
A modern CMMS/EAM is a different ball game altogether. In the digitalized IIoT domain, your work orders are managed on desktop PCs, laptops, smartphones, or tablets. On the go. Mobile and rapid. And failure reporting is simplified and made easy.
We at Dynaway realized that clients want faster and easier failure reporting. And what easier way to do this than failure codes.
Failure data is very important for leaders to make effective and efficient decisions. That’s why they are always looking for industry best practices and new implementation techniques to understand failure codes and failure modes in a better way. The organizations always focus on understanding failure codes so that they can design their CMMS… to better analyze the failure data.
John Reeve, Leveraging Failure Data for Better Decision Making (hpreliability.com)
A failure code – a.k.a. problem code – is simply a text or code to categorize an asset or component failure in the CMMS or EAM. Along with this, CMMS or EAMs like our EAM for Business Central also allow clients to input user-configurable Problem, Reason and Action codes.
And what could this look like in real terms if, for example, you had lots of pumps at your facility or installation?
Your technicians and engineers could navigate to the asset register or search open work orders, and then complete the feedback from an asset-specific drop-down problem code list for pumps:
Problem Code |
Meaning |
BRGSZD |
Bearing Seized |
IMPWRN |
Impeller Worn |
SELLKN |
Seal Leaking |
HGHVB |
High Vibration |
Reason Code |
Meaning |
LKLUB |
Lack of Lubrication |
CAV |
Cavitation |
UBL |
Unbalance |
MSLMT |
Misalignment |
Action Code |
Meaning |
BRGRNW |
Bearing Renewed |
FLTRPL |
Filter Replaced |
SELRPL |
Seal Replaced |
PRCNAL |
Precision Aligned |
Can you already see how you can quickly build up a clear picture of reliability and availability problems if you had several months or years of codes? By specifying different types of failures and reasons, you get valuable statistics that lead to analytics and insights that can set your business apart from the rest.
It's easy to get started with Failure Reporting
Most of all EAMs and CMMS have the facility for failure codes and, therefore, failure reporting.
But not all organizations use it.
Often this may be because the system wasn't set up with the input of a reliability engineer or maintenance professional. Sometimes unenlightened reliability engineers may not see the need for it and will happily accept long text fields.
This, again, is a shame.
With some simple tweaks, it's easy to create granular failure codes for each asset category so that technicians can choose from different asset-specific problems, reasons and action codes when repairing a gearbox, valve, conveyor belt, filler machine, and many, many other assets.
You may be asking yourself, but where can we get these codes? That's easy. You can get them by developing your own asset-specific FMEAs and convert your failure modes into codes. Or there are even organizations like OREDA that produce handbooks populated with failure modes and codes.
And once you've set up those codes on a system like Dynaway's EAM for BC, you'll be on the road to failure reporting in no time. Though, of course, you have to ensure that your technicians and engineers use the system as intended. With any change to a new way of working, don't forget to address the WIIFY!
What’s in it for you?
Your technicians and engineers will not adopt the new process if they don't see the value in it for them. Yes, that's a bit selfish, you may think. But that's how humans are! The WIIFY, however, should be a relatively easy sell:
- Less reactive maintenance and lying on their backs under that dark and oily conveyor.
- More proactive work: PMs, condition monitoring, defect elimination, root cause analysis.
- Less typing (Hint: drop-down lists!).
- Less overtime (refer to point 1).
OK, on second thoughts, maybe that last one should be kept secret.
With the right tools, failure reporting translates to reliability improvement
By now, you should be able to see the abundant value in failure reporting for your maintenance organization.
Plug the failure reporting data into a simple Pareto Analysis chart and see the 20% of assets that cause 80% of your maintenance costs or 80% of your downtime.
In the form of reliability improvement, value is also delivered to the bottom line by using the failure information for typical programs like FRACAS (failure reporting and corrective action system). This technique allows a coordinated and controlled effort at reducing asset failures and business costs.
You can also take advantage of the data for root cause analysis tools such as 5 Whys and cause and effect chart to understand the root causes of acute and chronic asset failures that keep on hitting the bottom line.
So, why not get on board with failure codes and failure reporting in the 21st century. Leverage the data in your systems and people. Come and speak to us at Dynaway to start on that journey.