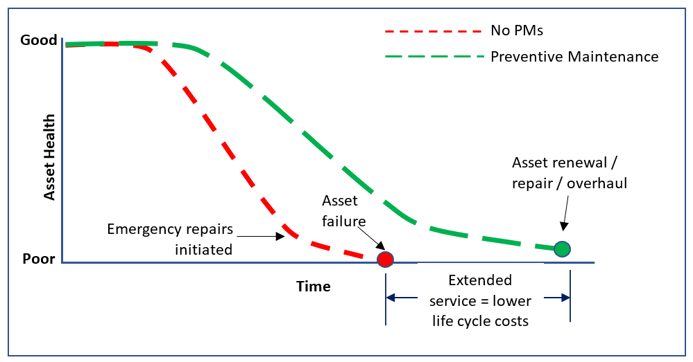
Preventive Maintenance Explained
Preventive maintenance (PM) is critical to profitability and performance in asset-intensive industries.
Every single PM task must provide a clear line of sight to the asset management objectives and organizational objectives. You have to know why you are tightening each bolt, why you are aligning each motor, and why you wash down each conveyor so often.
Each PM task must be value-adding and play its part in achieving high asset availability and preserving the inherent reliability of assets. Every PM task must provide a return on investment over the entire asset life cycle.
Before we get into the nuts and bolts, let’s take a step back.
What exactly is Preventive Maintenance?
Simply put, preventive maintenance is a strategy consisting of all the tasks performed by our maintenance and operations departments to prevent equipment failures and to preserve their primary functions.
You must have heard the acronym PM many times by now or even heard it called preventative maintenance.
But that’s what it is. The maintenance tasks that prevent failure of our equipment and preserve their operational function to deliver our saleable goods or services. It defends our organizations against those arch enemies: unscheduled downtime and production losses.
It has to be targeted at the right equipment and assets, and it has to be financially worth doing.
But more on that later.
Preventive Maintenance has a history
Here are some of the dominant industrial trends and companies over the last several decades:
Decade |
Dominant trends |
10s |
Industry 4.0 IoT. Maintenance 4.0. Circular economy and sustainable production, Google. Facebook. Twitter. Snapchat. |
00s |
Sustainable production. “Glocalization” (global + adapt to local). Industrial robots. GE. Microsoft. Intel. |
90s |
Globalization. Lean manufacturing, Six Sigma, RCM. Toyota, General Motors |
80s |
Automation, computers, electronics. Exxon Mobil, IBM |
70s |
Internationalization.
|
60s |
Mass-production. International trade. The Deming effect on Quality. |
50s |
Post war growth, increased consumerism. |
40s |
WW2 demands. |
Equipment was over-designed and straightforward in the time leading up to the 1940s. This meant it was generally reliable and easy to maintain, and reactive maintenance was the principal strategy. But during the 1940s, something changed dramatically. As WW2 raged across Europe, increased industrial demand meant downtime events were magnified. Equipment naturally became more complex and took longer to repair. Thus, preventive maintenance came to the fore in the form of scheduled overhauls.
The 1950s saw increased consumerism from the generation who survived the lean war years and further demand was placed on industry and preventive maintenance.
By the 1960s, mass production was in full effect and international trade was growing substantially – placing even higher demands on equipment. The ideas and influence of Edward Deming were having a profound effect on product quality, but scheduled overhauls and reactive maintenance were still dominant.
From the 1970s onwards came a need for higher quality and availability, less downtime, and longer equipment life cycles. Organizations had internationalized and needed to be globally competitive. Preventive maintenance had to add value, and it had to be worth doing. The realization came that scheduled overhauls didn’t always add value and didn’t always prevent failures.
Preventive maintenance had to move on.
New technologies such as condition monitoring were now in their infancy. PMs were more focused on cleaning, lubicating and inspecting.
The 1980s saw the boom of industrial automation, computers and electronics to drive operational efficiency. Along with this came a need for new maintenance skills, multi-skilling and new PM routines.
The 1990s saw mass globalization and the popularity of lean manufacturing and six sigma approaches to reduce waste and defects. Reliability-centred Maintenance (RCM) increased maintenance strategy understanding. And the 90s saw a drive towards operator-driven maintenance where the operators were expected to perform 1st line maintenance and PM tasks.
The focus shifted in the the 2000s to sustainability due to climate change and the term ‘Glocalization’ was born. By now condition monitoring technologies had advanced preventive maintenance significantly. Industrial robots had also come to the fore and brought new PM requirements with them.
The industrial landscape had changed significantly in the 2010s. Preventive maintenance found itself in a 4th industrial revolution (industry 4.0) where interconnected sensors and systems provided real time information on equipment health - though focus remained on sustainability and the circular economy. Technology giants dominated the landscape where their principal assets and equipment were data centres.
Nowadays, in asset-intensive and dynamic industries, we have a much better understanding of preventive maintenance and the way it adds value in achieving our organizational objectives.
We understand that allowing assets to fail - and then repairing them - is an expensive business. And that there are better ways to perform preventive maintenance.
Preventive maintenance is made up of different types of tasks
Some believe PM consists of only time or usage-based replacements. This is not strictly true. It’s only half the picture. Preventive maintenance can be divided into two main areas: time/usage-based maintenance and condition-based maintenance.
Time/usage-based maintenance
This is likely what springs to mind when you think of PM: Parts and components that are replaced or renewed on a time (calendar) basis or a usage basis. A process filter may be scheduled to be changed every 12 months or a paper-cutting blade may be scheduled for replacement after 2500 hours of service. In both cases, the items are known to wear out soon after those limits have been reached. And, therefore, the manufacturer is preventing failure.
Calendar-based tasks are much easier to schedule but they risk over or under maintaining the asset because there is no guarantee that the process filter has been used every day of that 12 months. On the other hand, usage-based tasks – though harder to track and manage - are more effective and economical as they are based on the actual utilization of the asset.
Other typical PM tasks such as cleaning and lubrication of assets can be considered as time/usage based activities. These simple - but critical – tasks are often performed on a scheduled basis in weeks or months of manufacturing activity and serve to preserve equipment function and reliability.
Condition-based maintenance (CBM)
This type of maintenance means that we perform a repair or replacement task based solely on the measured condition of an asset.
We use a technique called condition monitoring to allows us to carry out condition-based maintenance.
First, we measure a specific parameter of an asset’s health such as vibration, temperature, decibels, wear particles, or contamination. Then we trend the parameter value over time. When we believe it has reached a critical point that the asset is advancing towards a functional failure (it can’t perform its functions anymore), then we scheduled a condition-based maintenance intervention.
Here are some examples of CBM interventions:
- Replacing worn bearings
- Balancing fan impellers
- Renewing electrical contactors
- Aligning pump sets
- Replenishing lubricating oils
- Tightening loose electrical cables
CBM is the most cost-effective and economical way of maintaining assets based on real, actual deterioration mechanisms.
Condition Based Maintenance (component)
An equipment maintenance strategy based on measuring the condition of equipment against known standards in order to assess whether it will fail during some future period and taking appropriate action to avoid the consequences of that failure. The condition of the equipment could be measured using condition monitoring, statistical process control, equipment performance or through the use of human senses. The terms condition based maintenance (CBM), on-condition maintenance and predictive maintenance (PdM) can be used interchangeably.
SMRP Maintenance & Reliability Body of Knowledge Glossary.
A subset of the condition monitoring techniques is sensory and detailed inspections. They play a big role in preventive maintenance and the active highlighting of asset deterioration. Though they are often qualitative, we should always strive to make them as quantitative as possible. Sensory inspections can include the following:
- Listening for unusual noises.
- Looking for damage.
- Smelling for any signs of burning.
Detailed inspections (and checklists) can be used on all asset types and categories from a small 1kW dosing pump at a brewery to a 250 MW steam turbine at steelworks. Inspections can include the following:
- Ensure shaft runout is 0.004” or less.
- Inspect motor cable gland for signs of deterioration.
- Ensure drive belt tension is set to between 88 and 90 lbs.
- Inspect pump mechanical seal for leakage.
Now we all know what preventive maintenance means and what it consists of, it’s time to ask ourselves the next question.
What does good PM look like?
First up, it must be made clear that preventive maintenance does not apply to all assets. Most often,it will apply to the medium and high criticality assets at your organization. Low criticality assets are often run to failure because the consequences of their failure don’t justify the time and resources of PM.
Secondly, a discussion on preventive maintenance cannot be complete without stating that the best in class organizations use failure modes and effects analysis (FMEA) to develop their maintenance approaches and strategies – of which PM is always a key element.
Thirdly, manage your PMs in an EAM system or CMMS. Preventive Maintenance has its own workflow process as part of traditional work management. If you know your scheduled PMs, then you can forecast the resource planning and stay in control of costs.
Here are some best practices and pointers that will help you conduct proper preventive maintenance:
Time or usage-based PM – save these tasks for items or components that really do wear out over time. If you are replacing or overhauling items that do not show genuine wear out characteristics, then you are pouring money down the drain. Remember, this type of PM must be reserved for items that are in contact with the product or where friction is taking place.
CBM – your condition monitoring measurements should be taken at the right intervals for failure detection and should be based on detectable failure modes. By this we mean you are measuring vibration to highlight damaged bearings, misalignment, unbalance, or cavitation. It cannot tell you everything. And it will not tell you that have contaminated product going through your pump. Measurements must also be repeatable and collected from the same spot every time.
Inspections – your inspections program will be highly successful if it based on known failure modes, is quantitative and repeatable. Look at the difference here:
1a. |
Check the bearing for axial play. |
1b. |
Ensure all cap head bolts are tight. |
1a. |
Using a DTI, ensure bearing axial play is between 0.001” and 0.0015” at ambient temperature (18 to 30ºC). |
1b. |
Using a calibrated torque wrench in a crisscross manner, ensure all four (4) cap head bolts are torqued to 250 inch-pounds. |
Can you see how the second set of inspections are value adding?
In contrast, the first set of inspections are ambiguous and can lead to time-wasting, misinterpretation, arguments, and mistakes.
Nobody wants that!
Is Preventive Maintenance worth the effort?
We mentioned earlier than PM has to be worth it. And by that we mean financially worth the effort. The costs of preventing the failure have to be less than the costs of the failure itself – otherwise, it’s not .
Look at this diagram:
It shows a very simple concept.
If you perform very little PM, then your corrective maintenance costs will be high, i.e. you will have a lot of failures to correct. Conversely, if you perform excessive PM, then your corrective maintenance costs will be very low, but PM costs will soar upwards.
By understanding your assets, their failure modes, and maintenance needs, then you can find the sweet spot: the optimum maintenance interval. This is the PM interval that will deliver your organization the lowest maintenance costs over the asset life cycle for a specific PM task.
A similar concept regarding costs can be seen here:
It shows that by extending equipment life cycles through regular preventive maintenance, we can save significant life cycle costs in terms of operational and maintenance expenditure.
The moral of the story? Be planned and proactive, not totally reactive.
Things to be aware of
After all that good stuff, we must temper the discussion a little with things to be aware or wary of!
OEM recommended maintenance – if your asset is still in its warranty period, then yes, by all means follow the guidance. But be aware that after the warranty period ends you should review your PM strategy. This is because OEM recommended PMs are based on conservative estimates and worst-case scenarios. They can cause you to over-maintain your asset. This is because the OEM doesn’t know what industry you are in and it doesn’t know what the operating environment is.
And a further point to consider is that all OEMs make money on spare part sales.
Ambiguous, qualitative PM – be aware that PM inspections such as ‘check the pump’ leave your organization open to confusion, false calls, misinterpretation, and increased risk. Like we said earlier, make it value-adding and quantitative where possible.
Scheduled overhauls – If you are doing scheduled overhauls and replacing parts, then be absolutely sure that those parts you are replacing are genuinely wearing out through normal means. If you are replacing motors and gearboxes every six months - just in case they fail – then you are likely wasting valuable time, skilled resources, and money.
You don’t replace your car gearbox every six months, do you?
So that’s a great overview of preventive maintenance in terms of what it is, where it came from, best practices, and what to watch out for.
Where can you go next?
Those organizations that strive for operational excellence understand the need to embrace Industry 4.0 and the digitalization of maintenance. Preventive maintenance, its processes, and its workflows fit neatly into this new concept. Workers can now manage their PMs on the shop floor in real time with mobile solutions connected to the internet. Preventive maintenance dynamic data seen through the lens of industry 4.0 will open new pathways to data-rich decision making in your EAM or CMMS.
Make sure you cover all Maintenance Planning steps
Dynaway EAM for Business Central is a simple yet intuitive solution that is easy to use and helps you to bridge all the gaps in your Maintenance Planning.
Spend less time behind the computer and more time maintaining your assets!