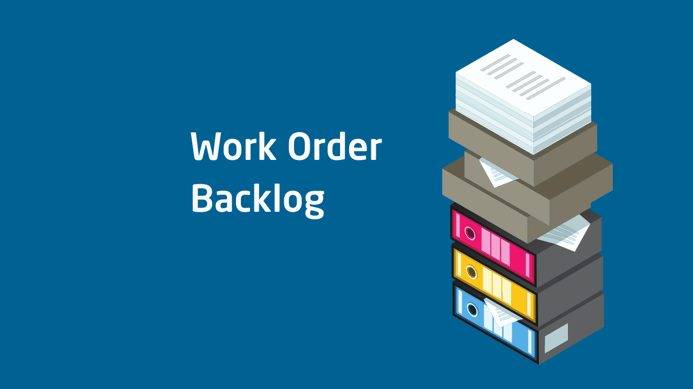
Crumbling infrastructure is a worldwide problem - spurred on, in part, by inaccurate predictions about the lifespan of things like bridges, and partially, from a global lack of sufficient funding for things like preventive maintenance.
Infrastructure maintenance isn’t an exciting topic, politically speaking, so the neglect is understandable - if reprehensible.
This has led to us - globally speaking - having a massive amount of work to do without the time or resources to do it all. A microcosm of this global phenomenon? Companies with an intimidating work order backlog.
Backlogs are good, actually
Before we delve into how you can conquer your backlog, there’s something we absolutely need to address:
Backlogs are good. When you have a backlog, it simply means you’re not doing all of your maintenance.
Maintenance staff need work, and there’s always work to be done. When you don’t have a backlog, you may not have sufficient work for your staff, which can lead to staffing shortages - a natural consequence of which is out-of-control backlog growth when work can’t be done. You absolutely want to maintain a backlog - a couple of weeks worth of work, at least. reactively. You should always have some form of preventive maintenance scheduled, as well as things like shut down maintenance to tackle those work orders that can’t be done when everything is up and running.
This article is dedicated to conquering and preventing excessive backlog.
Prioritize, then act
The first step to whittling away at that backlog is figuring out the most important work that needs to be done. More often than not, work orders are simply organized by the date they were scheduled, rather than by importance. Determine:
- Which of your assets are critically important to business operations
- Which assets are the most in need of repairs
- Which assets are the most in need of preventive maintenance
- What work can be done the most quickly/at the least cost
Use these metrics to prioritize work. For example, when faced with two critically important assets that are both in need of work, prioritize the one that’s easiest to do, freeing up resources for the more work-intense asset down the line.
Ask for more resources
This can be a tricky ask - there’s a tendency in some corporate cultures not to grant resources toward repairs when things are going well, and to blame facilities managers (and their staff) when things go badly. In either circumstance, getting the resources, you need to get through your backlog will take some explaining.
Go over the importance of proper backlog management - highlight the fact that if the backlog isn’t dealt with, reactive maintenance on critically important assets will become difficult, if not impossible. You should also focus on the fact that preventive maintenance (which we’ll address in greater detail soon) can seriously reduce a company’s overhead costs. Once you get buy-in, you’ll be able to work through your backlog much more effectively.
Organize your work orders
We’ve already discussed prioritizing work orders - organizing work orders is a bit different. This is the process of getting rid of duplicate or extremely low-priority work orders. It’s also the process of scheduling work orders so that work is distributed fairly to each team member.
Nesting work orders is another useful way of organizing - choosing to do all work requiring the same materials or on the same asset at the same time. In other words, if you’ve got preventive maintenance on a piece of equipment due at one time and a repair due a week earlier, do all of that work at the same time.
EAM/CMMS software can help with this - organizing and sending out work orders easily (or even automatically) is one of the core functionalities of these types of software.
Use predictive and preventive maintenance
Maxwell Davidson, the CEO of Maxpanda, has a great quote on preventive maintenance:
“There's never been a better time to set up preventative maintenance than right now.
It's the most inexpensive process you can apply to save on yearly costs.”
He’s right - preventive maintenance is like planting a tree. The best time to do it is 20 years ago, the second best time is now. Preventive maintenance works not only to reduce repair costs (reactive maintenance pretty much always costs more), it also makes the assets being maintained more energy-efficient and/or cost effective. Preventive maintenance could also be called restorative maintenance, because when done properly, it can restore lost functionality to assets.
Predictive maintenance is another excellent way to keep your backlog manageable once you’ve dealt with the excess. It’s basically preventive maintenance that uses AI to predict the cost of maintenance and the best time for maintenance, as well as the expected failure rate of a given asset (with and without preventive maintenance).
By using the tactics we’ve outlined here, you should be able to seriously reduce your backlog - and keep it down with preventive and predictive maintenance. An EAM software can seriously help with all of the above - by efficiently organizing and managing the administrative portion of your backlog, your team will be able to focus on actually getting the work done.