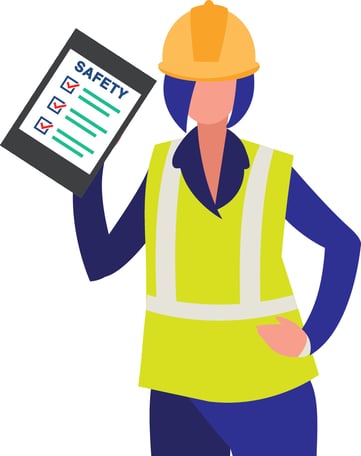
Managing your preventive maintenance can be a challenge. One of the best ways you can do it is the proper use of checklists.
Why do you need Maintenance Checklists?
Maintenance checklists have been proven to increase both preventive maintenance efficiency and overall safety in the facility. Maintenance checklists reduce the length of time needed to train new maintenance workers, improve communication between teams, assist with compliance and optimize maintenance practices. They allow for improved accountability and ensure consistency between team members. They can even reduce your energy bills.
If checklists can help you get everything at the grocery store, then they can help with much more complex Preventive Maintenance tasks. There are two kinds of checklists:
- The first is a pass/fail checklist, used to record factors such as outlet temperature and strokes-per-minute, then flag a machine for maintenance as needed.
- The second is a step-by-step maintenance checklist that ensures maintenance workers do routine maintenance in the correct order as well as reading and recording counters to transfer data to your EAM system or present it to the maintenance supervisor. These improve safety by ensuring that workers check off lockouts, testing, etc.
Your experienced maintenance workers may know these steps by heart, but you can't guarantee their availability. In fact, those senior workers are the people you should be tapping to help create the checklist in the first place. Checklists can also allow certain tasks to be done by machine operators and other less-trained people, so there's more time for maintenance and repair technicians to handle more skilled tasks.
What Maintenance Checklists do you need?
What checklists you need depends on the nature of your business, but here are some examples that most companies include:
- Daily checklists for each machine operator or driver so that they are always reminded of what they need to do, like: checking fuel levels, oil changes, etc.
- Preventive maintenance checklist and schedules.
- Routine equipment inspection checklist to ensure a safe environment in the facility.
These checklists can be dynamic and automatically include weekly or monthly checklists with a digital system.
Maintenance checklists need to be detailed enough that a brand new maintenance worker is given the information they need to do the task, but not so detailed they become lost. You can test this by giving the checklist to somebody in another department. They also need to come with time requirements, which should be generous enough not to rush people but realistic enough to keep them moving. All maintenance checklists should start and end with safety requirements to ensure that lockouts are done, and PPE is worn.
Checklists should be put together and regularly reviewed by the maintenance manager, but they should take impact from the manager, supervisor, and those senior technicians who know the checklists by heart. The last ensures that their institutional knowledge is not lost when they retire. It is important to listen to technicians. Sometimes they may adjust things because they do not see the point. Sometimes, they might come up with a more efficient way to do things that need to be reflected in the next version of the checklist.
How do digital Maintenance Checklists help?
Traditionally, checklists involved clipboards that might be carried by a technician or hung close to the machine. Digital checklists on Mobile EAM systems have a number of advantages over this:
- Physical checklists can be moved, lost, knocked to the floor, etc. With the EAM system, workers can simply use their phones to access digital checklists, making it less likely that a checklist will be unavailable when needed. Workers also do not need to go to a location to pick up a checklist to carry on the floor, which can also save a lot of time.
- A supervisor can easily see whether a checklist has been completed correctly on their phone or computer.
- Technicians can attach photos to the report to show the condition of the machine, allowing for greater accountability and helping senior technicians see what is going on before they go onto the floor. This can save a lot of time.
- Checklists can be automatically generated from templates and then customized for your specific equipment.
- Your EAM system can record data, track whether employees are completing tasks, tracking when machines break (and thus allow you to optimize maintenance schedules and create a better maintenance plan).
- Workers can use their phones to read a QR code on the machine, which automatically pulls up the checklist they need.
- The system can send alerts when a machine is due for regular maintenance, making sure that the right people know, or even add it to an individual worker's checklists.
- The supervisor or planner can quickly create a work order when an employee marks "fail"on a pass/fail checklist as data is handled in real-time. This can significantly reduce downtime.
- Digital checklists can easily include photos or diagrams to show new techs what the machine should look like. This can be complicated with physical checklists, especially when they need to be updated.
- For some facilities, significant amounts of paper can be saved by not printing off checklists, especially when they have to be updated fairly regularly.
A good mobile checklist system will allow workers to perform basic tasks even without an internet connection, uploading data as soon as there is a connection again. This is particularly important for construction sites and similar where connections can be spotty.
Mobile EAM is the easiest way to ensure that checklists are properly done, work orders are sent in as needed, and the data needed to optimize maintenance schedules is gathered and used.
Checklists are a vital tool to ensure that preventive and predictive maintenance is done on time, efficiently, and safely. They can reduce the cost of employee turnover, reduce downtime, improve safety, and ensure that you get the data you need to keep your facility running smoothly.