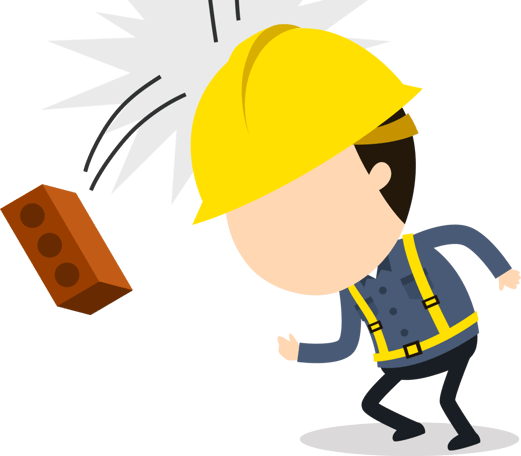
Walk around any typical industrial site and you'll see all sorts of maintenance work in progress.
- The particulars of the risk faced by workers and maintenance personnel can vary wildly between businesses.
- Mechanical work, electrical work, hot work and confined space are some of the safety permits most often issued in manufacturing and industrial environments.
- Work permits should always be issued for work activities subject to specific hazards.
- Precautions and safety measures should be addressed in the safe working procedure and risk assessment.
- Issued work permit certifies that the permit holder is prepared (in terms of training, experience and equipment) to manage the risks associated with whatever repairs or maintenance that must be conducted.
The clunking of spanners on bolts, multicolored electrical wires dangling from ceilings like twisted vines, welders' sparks flying into the air like miniature fireworks, towering cranes trundling along on their tracks … you get the idea.
All of those routine operations and maintenance tasks have their associated dangers. Such hazards, without proper precautions, can result in broken bones, electrical shock, burns and crush injuries — not to mention death. Not only are maintenance staff at risk, but any worker passing by areas where these operations are occurring may also end up in harm's way.
Safety permits and robust permit-to-work systems are essential for all of these different tasks, and risks need to be mitigated. Let's look into the specific risks, permit types and procedures that are necessary to ensure safe maintenance throughout your facility.
Major risk factors in manufacturing and industrial environments
While the particulars of the risk faced by workers and maintenance personnel can vary wildly between businesses, certain hazards are quite common in the heavy industrial world. First and arguably most prevalent is the machinery itself — hydraulics, pneumatics, tensioners, accumulators and so on — plenty of which can cause significant injury if stored energy is improperly released. Certain specific industries, including oil and gas, paper, chemicals and steelmaking, have ATEX zones in which flammable gases, vapors or combustible dust and debris can create explosive atmospheres.
Electrical hazards are also very common. Typical industrial voltages associated with systems and devices such as distribution boards, isolators, switches and busbars can range from 240 to 600 volts, depending on the asset application. Workers who come into contact with live cables are at risk of serious harm. (Industrial distribution voltage levels, meanwhile, are in the kilovolts.)
Along similar lines, there's "hot work" to consider: anything that involves burning, welding, cutting, brazing or grinding, as well as all operations that create a source of ignition. Hot work presents several hazards: welding fumes that can be inhaled, skin burns, welding arcs that damage eyesight and explosion risks if the work occurs in flammable atmospheres or near hazardous materials that cannot be removed. When uncontrolled or without a permit system in place, the risks and likelihood of an accident will be high. Anyone in the immediate and wider work area may be at risk — not just welders or grinders.
Some maintenance operations require pipelines to be opened. Personnel working on the lines are thus always at risk of being harmed by steam, corrosive liquids, dangerous gases, dust, flammable liquids and any highly pressurized substance traveling through pipelines. Initial risk can be quite high in process industries, with hazards ranging in severity level from minor injury to death, and accidents are highly likely if correct precautions aren't taken.
Manufacturing and heavy industry are environments with jarring extremes. For example, some maintenance tasks must be performed in a tight or confined space, where serious injury could occur due to hazardous substances or dangerous conditions within. Specific dangers include lack of oxygen, toxic atmospheres, oxygen enrichment and excessive heat.
On the opposite end of the spectrum, these industries may also require working with colossal machinery such as cranes, which are used in industrial settings for installation and removal of various assets. Though cranes come in many sizes, all of them carry suspended loads that, if dislodged or dropped, can crush and kill workers below. Other crane-related risks include contact with overhead electrical apparatus, collisions with nearby workers, and overload.
What are the common types of safety permits?
Work permits should always be issued for work activities subject to specific hazards like those described in the section above. The following are some of the safety permits most often issued in manufacturing and industrial environments:
Mechanical Work
A mechanical work permit is issued when maintenance staff must address issues affecting machinery with considerable amounts of stored energy. Personnel will isolate the equipment in question to keep any risks it poses away from everyday staff, through operations including valve isolation, flange isolation with spades and plates, purging of pipelines, implementation of lock-out-tag-out (LOTO) procedures and mandatory use of personal protective equipment (PPE).
Additional precautions include anti-static clothing, labeled zones, ATEX-rated electrical equipment and spark-free tools. There will still be residual risks when performing maintenance tasks in such situations, which should be addressed in the safe working procedure and risk assessment.
Electrical Work
Replacing a failed motor where humidity has caused insulation failure is a simple and common example of where an electrical work permit would be necessary. The motor must be electrically isolated for the power supply cables to be removed. If the power is not isolated, there's a very high risk of an accident.
In tandem with the use of PPE and permits (the issuance of which is contingent on an understanding of all risks and the proper procedures for mitigating them), the most typical precaution for electrical work is LOTO. Multiple locks can be used if several different maintenance team members need to work on the isolated equipment.
Although these actions will reduce risk, there is always the possibility of residual risks or incorrect assumptions about circuits being dead. Electricians must always test that "dead" circuits are isolated before working on them.
Hot Work
Hot work permits must be issued only to staff with specific training and experience in environments where such risks are common. Other typical precautions for this hazardous work include the use of barriers and cordons, fume removal equipment, fire blankets and extinguishers, PPE and the removal of nearby fuel sources wherever possible. There will always be some residual risk, but with a robust permit system in place, this should be tolerably low.
Confined Spaces
Although confined spaces can present a danger to all, only qualified personnel are allowed in through a proper permit-to-work system. When appropriately trained and experienced maintenance personnel enters such areas after receiving a confined-spaces work permit, comprehensive emergency procedures must be in place, with trained rescuers standing by and other personnel closely monitoring the work. Any ventilation that can be introduced will also be beneficial for work in tight spaces, and isolation of the area will help protect other workers in the facility.
Line Breaks
Line break permits are required if opening pipelines for cleaning and maintenance purposes. Precautions commonly taken to reduce risks associated with lines include the establishment of (and adherence to) safety checklists, LOTO procedures, purging of pipelines, flange isolations and the proper placement of barriers and warning signs in the immediate vicinity. If all proper precautions are taken and workers are constantly aware of the hazards they face, risk will be much lower.
Cranes
These permits (and those for other, similar machinery) are issued when maintenance staff must use them for specific operations. Only those with certifications or licensure from relevant industry organizations — such as the National Commission for the Certification of Crane Operators (NCCCO) in the U.S. — or government agencies (if applicable) will be given crane permits.
Other common precautions include lift plans, lift limits, training, barriers, weather assessments, close vigilance for warning signs of an accident and a bank person to guide the crane driver and lift. Even with all of these procedures in place, an extremely cautious approach is essential.
While the above overview of hazards and safety permits is by no means complete, it nonetheless illustrates that there are always a considerable number of risks to consider in manufacturing and industrial settings. Organizations with robust and reliable permit systems in place can reduce such risks to manageable levels.
Requesting and obtaining a permit
When a work permit is issued, it certifies that the maintenance team member holding it is prepared (in terms of training, experience and equipment) to handle the risks associated with whatever repairs or maintenance they must conduct. Because this is essentially a matter of life and death, it's critical that the process through which permits are issued be comprehensive and precise:
- Initiation: First, a work order goes out to alert the maintenance team to an issue requiring their attention. A risk assessment will follow, alongside a job plan detailing necessary steps, required tools and safety checklists.
- Permit request: A member of the maintenance staff will complete a request form containing details of the job (name, work location and duration, task details, date and time of the job, etc.) and submit it to the permit originator.
- Approval: As long as the maintenance won't interfere with other activities, the maintainer can then complete a permit-to-work form. This document should include more specific details on the maintenance work to be performed than what was provided for the request form, and a pertinent manager must approve it. Nearby employees, site security managers and control-room operators should be alerted before work begins.
- Work: Maintenance is performed, with all appropriate precautions followed to the letter.
- Sign-off or renewal: If maintenance is complete, the work permit is signed off. In situations where a task requires more time, the permit must be renewed until the job is done.
How EAM can streamline your permit-to-work system
Dynaway's state-of-the-art electronic asset management (EAM) platform within Microsoft Dynamics 365 offers Safe Work solutions for Microsoft Supply Chain Management (F&O) and Business Central platforms.
With Dynaway Safe Work you can make sure that all workers engaging in risky maintenance tasks receive appropriate safe work permits in a streamlined and efficient manner. This helps avoid costly non-compliance fines from regulators, minimize downtime and reduce the likelihood of accidents.
The Safe Work module allows users to manage permits as if they were paper forms. Permit templates make it easy to create customizable checklists, questions, drop-down menus and instructions for those filling in, approving and using permit-to-work forms. This creates a consistent process for requesting and issuing work permits. Permit forms can also be modified at any time, without affecting active or completed permits.
To learn more about the essentials of an effective permit-to-work system, download our eBook guide or contact us today.