
Maintenance is no longer just about replacing worn-out parts or doing a few repairs. With the increasing complexity of equipment and machinery, maintenance has become a critical part of any project lifecycle in an asset-intensive industry.
After all, you need to ensure that your equipment is ready for use every time you start up or even after an unexpected shutdown due to unforeseen circumstances like, for example, power outages.
Even though maintenance is one of the essential parts of running a business, it's no secret that it can also be challenging.
Along with many others, these 5 factors are holding companies back from reaching their full potential:
1. Asset Management
Asset management is the process of monitoring, controlling, and maintaining the lifecycle of an asset. It's a critical component of any maintenance program as it ensures that your equipment is operating at peak performance and in accordance with its intended purpose. That's why choosing the right EAM (Enterprise Asset Management) system that fits your business needs is critical to the success of your organization.
Read: 8 Key Questions IT Leaders Must Ask Before Purchasing a New EAM Software
Asset management can be challenging for a number of reasons:
- Complexity Asset management involves tracking and managing many assets, often with diverse and complex requirements, making it difficult to manage efficiently and effectively.
- Data Accuracy It's hard to ensure the accuracy of asset information as the data might be outdated, inconsistent, or spread across multiple systems.
- Integration Integrating asset management into existing systems and processes can be a challenging and long process, especially when dealing with legacy systems and data.
- Regulatory Compliance Asset management often involves complying with various regulations, such as environmental, health, and safety regulations, which can be complex and multifaceted.
- Resources Managing assets requires a significant amount of resources, including workforce, technology, and expertise, which can be difficult to secure and maintain.
.png?width=647&height=544&name=Untitled%20(800%20%C3%97%20673%20px).png)
Successful implementation of a suitable EAM solution could help your company solve the above-mentioned issues.
Enterprise Asset Management software allows organizations to track the location, condition, and maintenance history of assets while providing real-time visibility into the status of assets. It can help organizations to optimize their asset utilization, reducing the need for unnecessary replacements.
Moreover, it can be seamlessly integrated with other systems, such as Enterprise Resource Planning (ERP) or Customer Relationship Management (CRM). Integration supports data consistency and accuracy.
2. Maintenance Scheduling
Maintenance activities need to be scheduled to minimize downtime and maximize the equipment's efficiency. This can be challenging, especially when dealing with numerous pieces of equipment and limited maintenance staff. Organizations may use specialized software to help schedule maintenance activities, but coordinating everything can still be difficult.
The most important thing to remember when scheduling maintenance is that it should be done on an ongoing basis. This means routine inspections and repairs should be performed every few weeks/months/years, depending on what kind of equipment you are working with.
The Maintenance Planner/Scheduler must consider all aspects of the equipment, including its life expectancy and maintenance requirements.
His paramount responsibility is to plan and schedule the maintenance activities, assign them to the maintenance workers, determine which tasks require special documentation (permits), and provide the documentation to the right personnel. Many things can go wrong, but it's a false estimation of work order time that is causing delays and unavailability of resources.
To estimate the work order time accurately, you can:
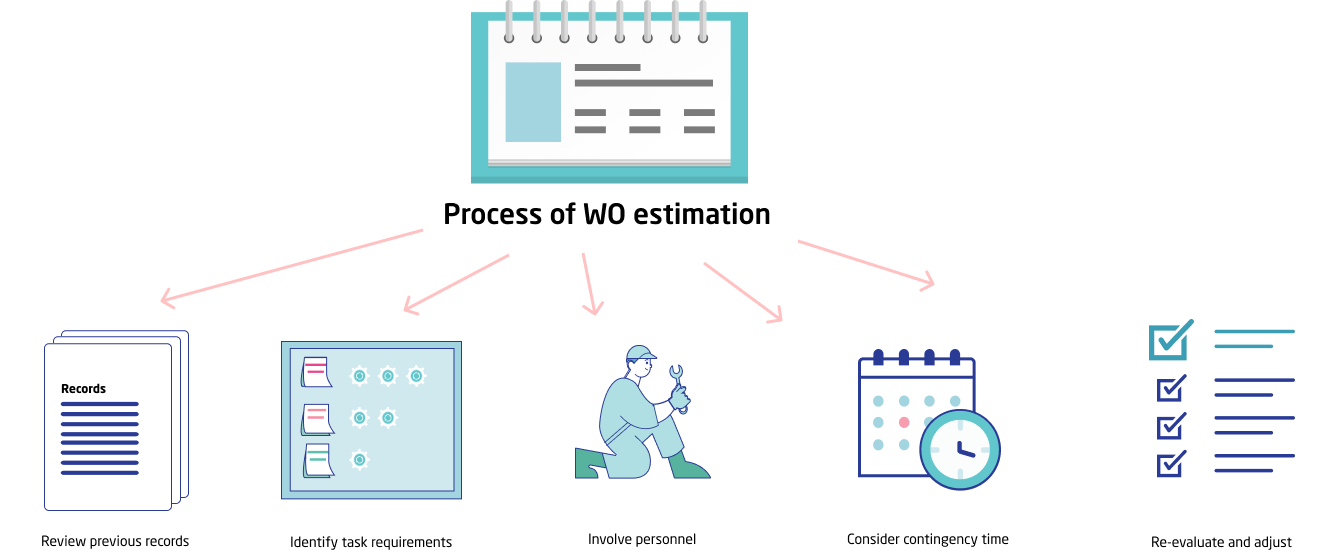
- Review previous records Look at previous records of similar work orders to determine the time required to complete similar tasks.
- Identify task requirements Clearly define the scope of the work order, including materials and tools required.
- Involve personnel Collect insights from the employees who have experience with the specific work type.
- Consider contingency time Add a contingency buffer to the estimated time to account for unexpected events, such as equipment failures or inclement weather.
- Re-evaluate and adjust Regularly re-evaluate and adjust the estimated time as the work order progresses. This will help to ensure that the estimated time remains accurate and that the work order can be completed on time.
3. Cost Management
The cost of maintenance is often underestimated.
Many managers are not aware of the costs associated with their maintenance program and therefore do not have a clear picture of how much money they need to invest in order to keep their equipment running smoothly, or even if it's worth the investment at all.
To help you manage your costs better, here are some tips:
- Understand what goes into each repair job - this will help you determine whether an item really needs to be fixed or can simply be replaced instead. For example, if an air conditioning unit has broken down because one part needs replacing but there are still other parts that work fine (and aren't malfunctioning), then maybe it wouldn't make sense for you to replace everything at once just because one part is broken.
- Schedule regular inspections so any equipment issues can be detected early on before they become costly problems. Later on, it may already be too late for repair attempts - some parts might already have been damaged due to neglect over time. Especially when we're talking about machines that require regular upkeep (like cars do); so always make sure those "cars" stay clean inside out too.
Finding the right balance between cost and quality while maintaining a competitive cost structure is difficult. Thus, it's important to establish clear cost management goals and objectives, implement cost control measures and tracking systems, and continuously review and adjust budget and cost estimates.
If you're looking for more guidance on the topic of cost management, check out our article: "8 steps to reduce Maintenance Management Costs"
4. Technological Advancement
The rise of technology has given us many things, from the ability to look up recipes on our phones and order food through a delivery service to automated cars and robots that can vacuum our houses. While these advances are great for our everyday lives, they can sometimes cause issues in the rapidly changing maintenance world.
New technologies emerge and old ones fall out of favor, which implies that companies need to stay on top of these changes to succeed in their industry.
However, it takes work.
Implementing changes in the organization brings many difficulties. It requires careful planning,adequate resources, and effective communication with all stakeholders. It is essential to understand the impact of the change on all areas of the organization and to ensure that everyone is prepared and has the necessary support to make the transition as smooth as possible. Here comes the technology training.
Training is required to gain a deep understanding of the technology involved. Invest in training for the most critical technologies - identify the technologies that are most critical to your business operations and invest in training for those technologies first.
Consider partnering with vendors or industry experts - it can be more cost-effective than developing training programs internally, as it leverages the expertise and resources of others. Besides, vendor and industry experts are often at the forefront of new technological developments and advancements and can provide up-to-date information. Highly experienced professionals can provide high-quality training tailored to your organization's specific needs.
Remember to regularly evaluate the effectiveness of your technology training programs and make adjustments as needed to ensure that they fulfill the needs of your employees.
.png?width=847&height=513&name=Untitled%20(760%20%C3%97%20460%20px).png)
5. Safety
Last but not least - safety is a priority for everyone.
It begins with leadership and commitment from management to create a safe environment through policies,training programs,communication channels, as well as asset maintenance schedules that keep maintenance workers safe while performing their tasks.
Maintenance work often involves:
- Handling heavy machinery.
- Using hazardous materials (such as chemicals, fuels, and lubricants).
- Working with electrical equipment.
- Working at heights.
Besides, maintenance workers often work long hours and under pressure, which can increase the risk of fatigue and stress-related incidents.
It's not new to say that maintenance activities can be particularly dangerous if appropriate safety measures are not in place. Therefore, it's important to include safety in your maintenance planning process by considering:How will you keep workers safe?; What types of hazards do you need to address?; How will you identify these hazards and eliminate them?
Permit-to-Work (PTW) system can be a way to control hazardous work. Many Safety Managers ensure the application of suitable PTW systems in their companies in order to:
- Allow the stakeholders to be aware of the potentially hazardous activities that are being undertaken;
- Set limits to the duration and extent of work;
- Define the controls required to prevent threats from releasing hazards during the work
- Encourage formality and attention to a safe way of work by requiring the signature of specified individuals who must confirm satisfactory completion of the various stages of the PTW lifecycle.
Regardless of whether you have a system implemented or not, as an employee, you should remember to:
- Report any potential hazards immediately; this includes anything that could cause injury or illness, such as slippery floors or broken equipment (even if it isn't yours). Your supervisor should address these issues immediately so they don't become more significant problems later on down the road.
- Stay alert while working - don't get distracted by things like your phone/computer screen; instead, focus on what needs doing right now! This way, nothing slips through the cracks - you'll always know exactly what needs doing next without having any surprises waiting around the corner. Most accidents happen when people are not paying attention or don't think about their actions enough before they do them.

Challenges in the maintenance world are real, but they can be managed
Taking care of the assets is a top priority in the maintenance world. While there may be a few challenges along the way, like keeping equipment organized, making sure work orders are on track, and ensuring safe working conditions, the good news is that there are solutions!
By using tools like asset management systems, organizations can make maintenance a breeze and keep their assets in tip-top shape. With these helpful tools, you can say goodbye to downtime and hello to happy and productive assets.
If you want to learn more about how you can incorporate technology to make your operations more efficient, contact us today or check out more of our resources.