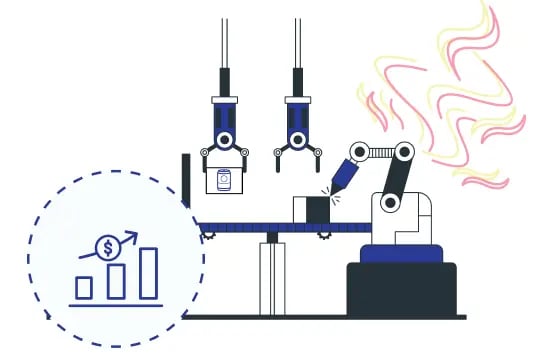
Being a maintenance manager in today’s world is a tough gig. Ask one what it’s like if you know any. You’ll get a roll of the eyes, sunken shoulders, and a stressed complexion.
If you are a maintenance manager, you’ll be thinking about late-night calls interrupting your sleep, cranky - passive-aggressive - morning meetings, breakdowns being pinned on you as a badge of shame, and the eternal fight for a reasonable budget.
But "maintenance is a cost to the business", they say.
The Cost of it All
The maintenance department is a profit-center when done well. But it must be planned well, done well, run well, and not a living hell. Mistakes in maintenance or the approach to it can be very costly to the business whether it’s manufacturing toys or commercial airplanes.
So, what can you do?
Save Yourself Money
There are common mistakes that maintenance managers make – young or old – and which, if rectified, can be a real source of cost reduction, failure elimination, and improved asset availability. Here’s our take on the 7 most common mistakes that maintenance managers make:
1. Not having a planner or scheduler on your team
There are many manufacturing plants and industrial enterprises that don’t have a planner or scheduler dedicated to maintenance workflows or, worse than that, a part-time planner who is also a store controller and maintenance supervisor for good measure.
Having no dedicated person to plan corrective and planned maintenance, obtain spare parts, and organize special tools, contractors, and permits, will result in chaos. And chaos results in spiraling costs and a lack of control over maintenance. Work orders will not be prioritized; they will be a free-for-all.
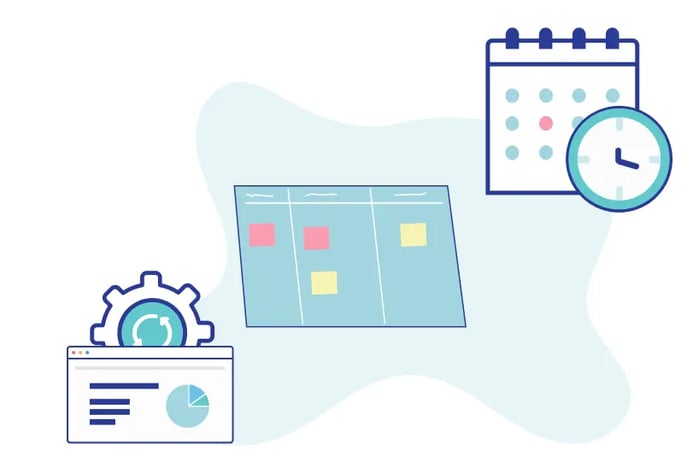
Some plant managers don’t believe a planner/scheduler is necessary. ‘Another head is too expensive’ they say. This is a false economy. A planner and scheduler – combined or alone – are worth their weight in gold. Not having one will overload a maintenance manager and choke the workflow.
Solution: Get your department a maintenance planner and scheduler as a minimum. Combine the role for smaller plants.
2. Not acting on PM inspection feedback and Condition Monitoring recommendations
Now, this ties in with the planning function, but the maintenance manager must drive it and monitor it. If the results of inspections are not acted upon, then the plant will remain in the reactive failure cycle and the increased costs that come with it.
Asset condition degrades over time. So, if all those leaks, squeaks, noises, and overheating are not corrected, then risks increase and performance reduces. And what’s more, the maintenance technicians reporting these issues will lose faith in maintenance management and lose interest in the strategy. PMs and condition monitoring (CM) inspections cannot – must not – be a tick-box exercise.
When the big failure happens, your technicians will give you that look: I have been telling you so.
Solution: Proactively drive the follow-up and planning of remedial maintenance from PMs and CM inspections.
3. Spending too little time on the shop floor
Although difficult to put a cost on, this one has long-term intangible benefits.
If you’re a professional desk jockey, you may be asking what’s the problem? Well, being locked up in an office all day will mean this:
- You won’t engage with your team or with operations.
- You won't exercise your leadership on the front line.
- You won’t see the recurring issues - and pain - close-up.
- You won’t get asset knowledge (‘Hey Jeff, what’s that clanking noise on the B221? I think the X9 shaft bearing has gone again’. You sheepishly reply, ‘What’s a B221?).
Solution: Spend at least just a little time each day on the shop floor. Talk to people. Show interest. It will pay back in many, many ways.
4. Not developing and empowering your maintenance team
Training and development are critical to the functioning, stability, and growth of any business. Not only that, it’s of supreme importance to employees. Without adequate and ongoing training, they feel the lack of growth, a lack of interest in them; it will degrade your department's culture and apathy will replace enthusiasm in even the most optimistic person. Concurrent with this, your business runs the risk of losing talent. And that’s costly.
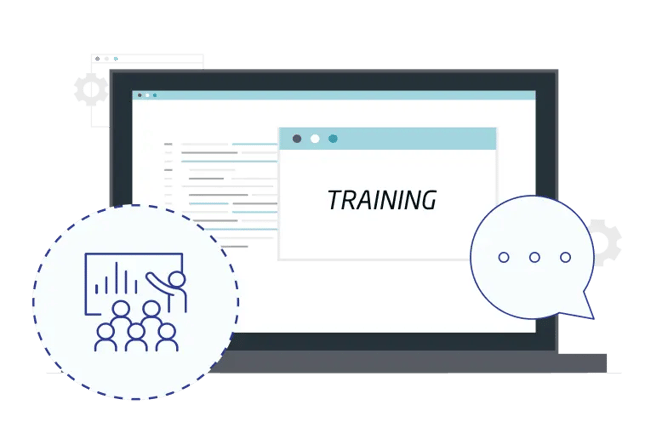
With a lack of training, maintenance mistakes will be made. If you don’t train them to fit the flexi-link conveyor belt properly, then breakages and stoppages happen. If you don’t train them to look after the gas-fired boilers properly, then the unthinkable can happen.
Solution: Get a training plan in place - based on roles, responsibilities, and mandatory requirements - and deliver it in full.
5. Rewarding the fire-fighting mindset
This is a big one.
Imagine…
…a critical pump fails Saturday night at 11.30 p.m. The plant’s on stop. There’s no maintenance cover, so you call in Frankie – again - to save the day (or night). Frankie fixes the pump, gets overtime at a triple rate, and gets home by 3 a.m. On Monday you thank Frankie, tell the management team what a great job it was, and put a little story in the company magazine. Maybe even a recommendation for employee of the month.
Many maintenance managers do this. They may think it’s helpful, but it’s not.
Rewarding firefighting produces a counterproductive mindset and culture; it continues the reactive cycle because it motivates the team to stay reactive for tangible and intangible rewards. Increased overtime becomes the new normal.
Solution: Reward adherence to PMs and schedule compliance. Reward technicians for proactive maintenance and defect elimination using RCA and continuous improvement.
6. Failing to monitor the CMMS/EAM system
Whether a CMMS (computerized maintenance management system) or EAM (enterprise asset management) system is used, a maintenance manager needs to monitor it closely to make sure it’s in the best shape it can be. It is fundamental to the success of the maintenance department.
It is fundamental.
If you fail to monitor – and assure - the quality and content of the asset register, PMs, and work orders, then you are working against maintenance excellence. The CMMS/EAM is the literal heartbeat of a maintenance department. If you have a poor asset register and inferior and ill-thought-out PM tasks, then you are in trouble. Does this work order feedback seem familiar?
Pump broke. I fixed it. All OK now.
If so, you must intervene soon. This lack of information, lack of failure modes, and engineering detail is paralyzing. For improving things, it is close to worthless. No reliability improvement can ever be gained from it. Availability and reliability continue to suffer, costs continue to spiral…
Solution: Monitor the CMMS/EAM for a full and authentic asset register. Get the right PMs in place. Get failure modes included on the work order.
7. Not engaging and aligning with the Reliability Engineer(s)
The maintenance department can often be seen as a slightly detached - occasionally maverick - group of people. But the department must interact with others if the corporate or asset management plan is to be achieved.
To be a successful maintenance manager, there is a key person you need to work with: the reliability engineer.
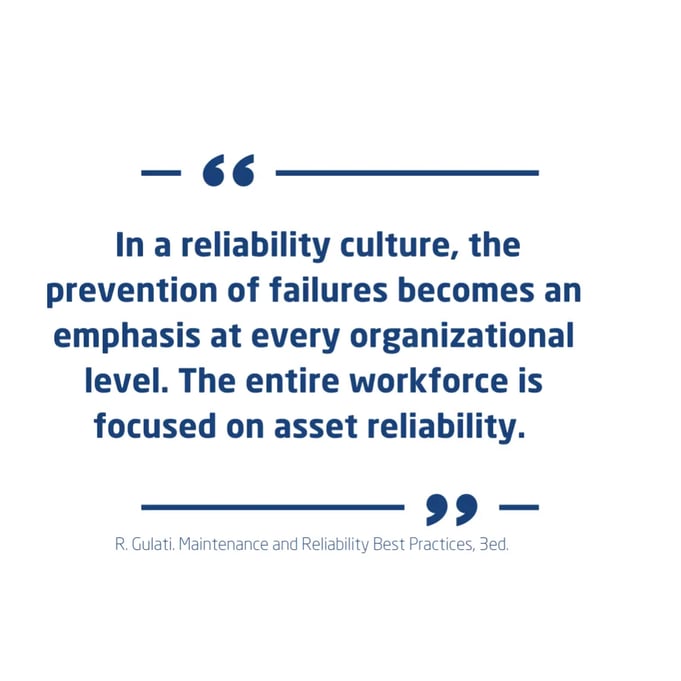
She or he will help you deliver a professional maintenance strategy like RCM, facilitate FMEAs with your team – and engage them - and train the department in RCA methodology. All this increases plant availability and achieves a more reliable plant: operating costs go down.
Solution: engage and align with the reliability engineer(s). They want the same things as you do and will help you get there.
It’s All About the Costs in the End
You’re a maintenance manager. You’re in a business. The goals are always profitability-related.
Pay attention to these 7 expensive mistakes, and you’ll be on the way to a better night’s sleep, more pleasant morning meetings, fewer breakdowns, and – if you’re really lucky - less resistance to your maintenance budget requests.