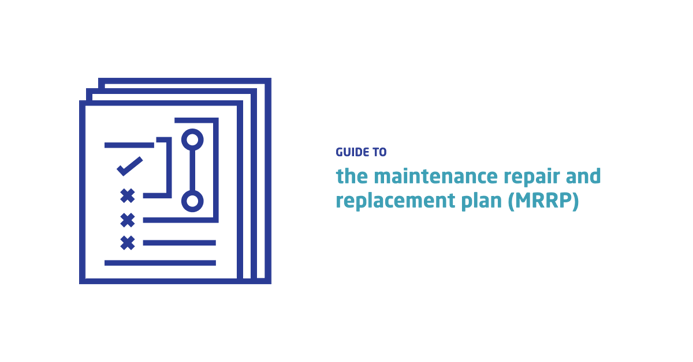
Every maintenance department knows the importance of preventing asset failure. It’s how you stay productive, maximize uptime and prolong the life of your critical equipment.
And when you’re talking about critical production equipment — those that are key to producing your company’s output — asset failure is all the more significant. To ensure your facility’s maintenance tasks are performed properly and according to schedule, you need a maintenance repair and replacement plan.
In this guide, we’ll discuss the ins and outs of the maintenance plan and what you can do to optimize the process.
What is a maintenance repair and replacement plan?
How much does it cost to replace an elevator? How much does it cost to patch up a roof? What tools will you need to fix a broken piece of equipment? Who’s going to complete all that work, anyway?
These are the types of questions you need to be able to answer when creating a maintenance repair and replacement plan (MRRP). Simply put, a maintenance repair and replacement plan is a detailed 10-year report that outlines the planned maintenance procedures of the common property (i.e. your facility).
It’s the responsibility of everybody corporate to prepare this maintenance plan to ensure that all maintenance projects are completed, appliances are refurbished, and that no components pose a risk to health or safety.
Why? Because a poorly designed service plan inevitably leads to poorly executed maintenance tasks. To prevent these mistakes, here’s a breakdown of the essential information you should be including in your MRRP:
- The major capital items and equipment expected to require maintenance work or replacement within the next 10 years.
- The current condition of those items.
- When those assets will need to be maintained, repaired or replaced.
- The estimated cost of those items, parts and equipment.
- The expected lifespan of those assets once they have been maintained, repaired or replaced.
With this information, you’ll be able to properly determine your maintenance needs over the course of that timeline. This will help you identify which type of maintenance you’ll need. These types include:
Corrective maintenance
Corrective maintenance includes any maintenance task that is performed to repair or restore equipment after asset failure.
Preventive maintenance
Preventive maintenance includes any planned maintenance activity that intends to prevent unplanned downtime and keep assets up and running for as long as possible. Preventive action has shown to yield considerable cost savings for organizations – between 18% and 25%, per McKinsey – on maintenance expenditures alone, with further savings resulting from increased asset availability.
These categories can be further broken down into several subcategories, such as emergency maintenance or time-based maintenance.
Stages of the maintenance repair and replacement planning process
When it comes to compiling an effective 10-year maintenance plan, there’s obviously a lot of moving parts and factors to consider. Though it can be a difficult and time-consuming process, it’s essential to the longevity and safety of your facility.
Making the most of this initiative is all about knowing what to expect along the way. Here are the basic stages of the maintenance repair and replacement process:
- Inspecting the property: Performing a comprehensive inspection of the facility, your assets and production equipment will help you forecast maintenance cost and optimize your service plan.
- Forecast and analysis: This is where you compile a report that includes a life cycle cost analysis, your 10-year cost forecast and a schedule of maintenance projects.
- Preparing the MRRP: Now, you translate your findings into an actionable maintenance plan.
- Carrying out your tasks: Once your plan is approved by the body corporate and trustees, you can proceed with maintaining and replacing assets as necessary.
Importantly, the MRRP should be a living, flexible document. By updating your service plan on an annual basis, you can adjust your planned maintenance activities or add new ones as required. It’s also important to update your plan as tasks are completed to maintain accuracy.
If you fail to update the MRRP, this error has the potential to yield several cascading effects. For example, an out-of-date MRRP prevents trustees from accurately tracking capital expenditure, which may lead to a lack of funds available for planned or emergency maintenance tasks.
What are the benefits of a 10-year maintenance plan?
Implementing a 10-year MRRP may be a tedious process, but it’s well worth the effort when you consider the benefits.
Benefits of MRRP
- Improved financial planning.
- Better transparency of body corporate affairs.
- Maintenance projects are assigned their necessary resources.
- Plans ensure that critical equipment can be maintained on schedule to avoid unplanned downtime.
Leveraging technology for a smarter approach to maintenance
Considering that downtime is known to cost organizations enormous sums of money, it’s no surprise that many are doing all they can to prevent asset failure in the first place. Remember: Your facility is just as much an asset as any spare part or piece of equipment.
That’s why businesses are racing to invest in smarter solutions. According to IBM, most companies expect investments in technology to reduce downtime, increase revenue and improve employee productivity.
One such solution that’s poised to streamline the maintenance planning process is a Computerized Maintenance Management System (CMMS). A CMMS centralizes all of your maintenance procedures – including planning, scheduling and resourcing – into one single-pane-of-glass view.
Take warranties, for example. A CMMS solution tracks warranties to ensure that broken-down equipment can be repaired or replaced as efficiently and timely as possible. This not only minimizes maintenance costs but also accelerates the maintenance process.
Likewise, an Enterprise Asset Management (EAM) solution can simplify the decision-making process, track your spare part inventory and so much more. Dynaway’s Microsoft Dynamics 365-based EAM platform leverages ERP data to your advantage for maximum uptime and efficiency.
To learn more about Dynaway’s enterprise asset solution, check out our comprehensive EAM tool today.