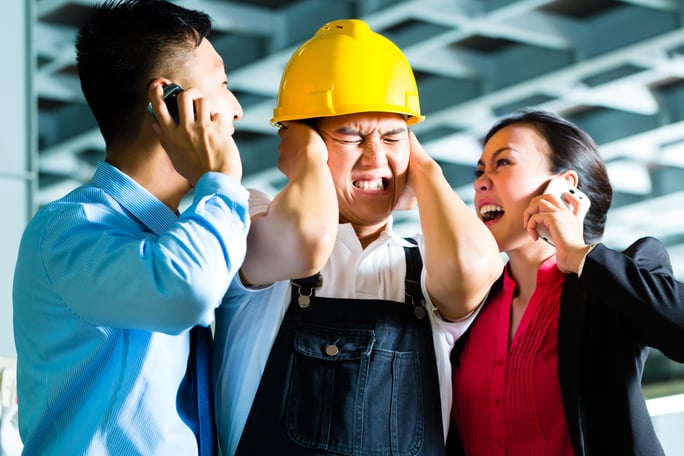
Equipment maintenance is a cornerstone of facilities management. The scope and complexity of that work — and the degree to which it will cause equipment downtime — depends entirely on the maintenance plan your organization has in place.
Reactive maintenance is among the most common types of maintenance strategy seen across numerous industrial sectors. This doesn't, however, mean that it's necessarily the right choice, and it may even be a truly bad idea for your facility, due to the potential for adverse effects over long periods. It's critical that you take the time to truly understand the reactive maintenance cycle and the numerous alternatives to it instead of resigning yourself to the idea that it's the sole appropriate maintenance method for your needs.
What is reactive maintenance?
Reactive maintenance efforts have another well-known name: breakdown maintenance. As the latter term implies, in this model, the maintenance team does not service a given piece of equipment until it fails. The reactive strategy is in direct contradiction to the principles of preventive maintenance, which involves tackling maintenance issues as an ongoing process, and checking asset health regularly (even when all signs indicate that machinery and devices are in proper working order).
Reactive repairs are also different from the corrective maintenance strategy. By the principles of the latter, you would repair an asset only when it was malfunctioning. There are many degrees of malfunction, of course: This could be a problem that partially impedes the expected performance of a piece of equipment but doesn't stop it from working entirely. Or it could be a problem manifesting in such a way that the safety or lives of personnel — or the integrity of machinery connected to it or just near it — are put in jeopardy. (Some would call that effectively reactive, not corrective; we leave that up to the perspective of the individual.)
In the introduction, we alluded to the fact that most of the organizations using the reactive model as their sole maintenance operation framework do so to cut costs. It certainly has that effect when your facility is in good shape; you spend no immediate money by not repairing a machine or vehicle, after all. That lack of initial cost can be incredibly tempting.
It's also much less time-consuming and resource-intensive to not put effort or labor toward maintaining unbroken equipment, i.e., using spare parts and labor on a machine that's still running. Furthermore, one must note that if utilized as one part of a larger maintenance activity plan, there can be a reasonable argument for the use of reactive repairs — in moderation and/or where most appropriate to a specific situation. If the equipment in question is fairly low on your facility's priority list, and will not take long or cost a lot of money to complete an emergency repair, being reactive might be better than (or at least equivalent in result to) a proactive approach.
Unfortunately, organizations with their priorities focused in other areas or that are experiencing budget problems may put maintenance as a whole on the back burner, meaning they're only performing emergency repairs when absolutely necessary. This is where the trouble starts to brew. Using the reactive maintenance method and repairing assets only when equipment failure occurs might make sense when you consider it in the abstract. But it quite simply can't be your main method of approaching maintenance.
The problems of reactive maintenance
Reactionary or reactive maintenance is, in the long run, a shortsighted approach for any factory or plant. It cannot be sustained over any long period of time, as it's bound to eventually lead to negative results of some sort. The specifics of these issues vary by industry (and, even more so, from facility to facility), but generally speaking, there are several key problems that can often be attributed to the impact of a reactive maintenance method.
High cost
This is the great irony of a maintenance program that is reactive rather than proactive or preventive: Although reactive maintenance is typically implemented as a cost-saving measure, it can become an expensive boondoggle faster than you might think.
How so? The main issue is unexpected downtime. When you're using the reactive method, you aren't watching closely for signs that a machine is experiencing problems that will eventually result in asset failure. You weren't planning for any of this and didn't have any contingency plans in place, so delays are inevitable. The slowdown of critical facility processes that result from failed pieces of equipment can lead to bigger production problems. Those, in turn, can snowball into damaged or lower-quality goods, late deliveries and disappointed customers.
All of those things can negatively affect revenue — most notably the displeasure of your clients. Losing them might not just mean the loss of their purchases. It could quickly become a negative word of mouth that damages your organization's reputation, potentially causing you to hemorrhage more of your customer base and jeopardize your bottom line even more severely.
On the less dramatic (but still quite problematic) end of the sunk-cost spectrum is your labor and parts budget: Relying on reactive maintenance means that the price of labor and spare components might not be forecasted accurately. This could mean you aren't even able to afford your reactive repairs — which, because you waited until the last minute when the asset failed, you have no choice but to make.
If you don't have the capital on hand to foot the bill because expenses have gotten out of control in this scenario, you might be stuck looking for short-term lines of credit or other financing: Going that route, will only cause more trouble somewhere down the line. Even in a better case scenario, your company will still end up losing money due to the need for emergency expedited shipping of essential parts and overtime pay for maintenance personnel.
Last but not least, equipment that isn't well-maintained uses more energy than it would if it were regularly checked on as part of a preventive maintenance program. This occurs because the device has to "work harder" to function normally, which draws more power than usual and makes for yet another unforced (and costly) error.
The lowered life expectancy of assets
When you only resort to repairs because failure or near failure has made them absolutely necessary, you're not keeping your equipment running in an optimal way. By extension, you're not maximizing your company's initial investment in the machinery or other assets. Equipment is thus more likely to fail for good faster than it ordinarily would, and over enough time, the price of replacing assets "before their time" can become an absolute money pit.
Reduced safety
In a preventive maintenance strategy, work orders for asset repairs or checkups are either scheduled precisely at regular intervals or determined by ongoing condition monitoring. Workers in both scenarios have the time to prepare for the job and — perhaps most importantly — review standard procedures for maintaining specific machines. Every asset has safety requirements that should be observed to complete the job correctly.
With a reactive maintenance strategy addressing unplanned repairs, everything is more urgent. Workers are under pressure. As a result, they may feel like they have to take more risks to get the job done quickly. Not only does this jeopardize their safety, but it's also unfair to employees from a purely human perspective. A worker who feels constantly under pressure, or that their concerns aren't being addressed, is more likely to become disengaged and perform less effectively.
Time management
Failures occur unexpectedly when you use the reactive maintenance approach as your go-to repair strategy. Workers run around looking for the correct safety documentation — as well as spare parts and tools — and often aren't able to complete maintenance tasks quickly no matter how much pressure they're under.
Establishing a better routine for equipment maintenance
If you've been using the reactive strategy, there's no reason to feel as if your organization is stuck with it. You can transition to a preventive maintenance model of facilities management — perhaps not instantaneously, but with the right perspective and tools, a more efficient model is achievable.
Preventive maintenance can best be expressed by the principle of "forewarned is forearmed." This starts by zeroing in on the right key performance indicators to monitor among your assets, as well as a priority list of the most vital equipment. You'll find that not only will a broad shift in maintenance philosophy be beneficial but also that even seemingly minuscule changes can make major differences over time. For example, simple acts of routine machine maintenance like greasing some gears or changing filters can reduce energy consumption by as much as 15%.
The Dynaway enterprise asset management solution, seamlessly integrated into Microsoft Dynamics 365, can also be part of how you build your way to a better, more efficient maintenance framework.