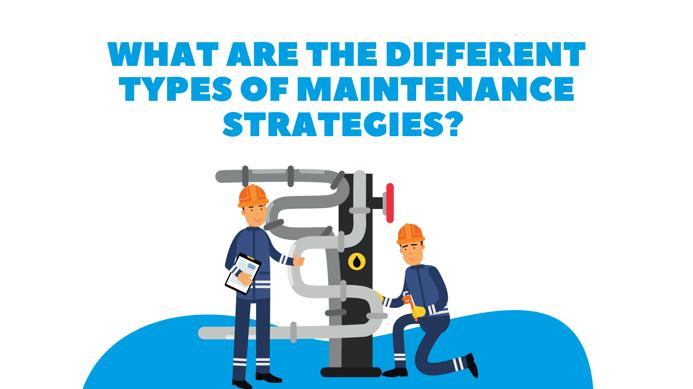
Maintenance is an essential part of any facility’s equipment infrastructure.
When critical assets degrade or break down beyond repair, important business functions are curtailed and disrupted.
That downtime, in turn, becomes a costly headache that tanks productivity, particularly if the issue is so severe that replacement is necessary.
Reducing the extent of that disruption — or, preferably, preventing it entirely — largely depends on the organization's chosen approach. When it comes to maintenance, shooting blind only gets you so far. Employing a strategic ethos is the best foot forward when maintaining your vital assets.
Of course, with so many approaches to choose from, deciding on any one solution is no easy task. Here, we’ll guide you through maintenance strategy and the many options you have at your discretion.
The importance of a strategic approach to maintenance
When it comes to maintenance operations, the best ability is reliability. Organizations rely on their equipment to perform critical business functions. When asset failure occurs, unplanned downtime is detrimental to productivity at large.
It should come as no surprise that the most optimal way to mitigate asset failure is to avoid it altogether. In a nutshell, that’s what a maintenance strategy aims to achieve. By devising and implementing a thorough, company-wide approach to asset management, you can eliminate inefficiencies and ensure that critical operations are performed consistently. Indeed, there are many directions an organization may explore.
Yet, employing any maintenance strategy is better than taking no strategy at all. With a haphazard hit-and-miss approach, maintenance is much too chaotic, problematic and disorganized to be effective. Consequently, suboptimal asset management puts the business — but more importantly, the workforce — at substantial risk.
In turn, deciding on how your facility will strategically approach equipment maintenance is one of the most integral business decisions an organization can make. However, it’s unlikely that any single strategy will fit perfectly into your specific asset infrastructure. Rather, according to research from Michael Guy Deighton, the selection process more often involves a combination of maintenance strategies. In simpler terms, mixing different tactics is the best way to identify the most optimal approach to your organization’s specific maintenance activity.
What are the different types of maintenance strategies?
Broadly speaking, there are two big umbrella categories when it comes to equipment maintenance strategy: preventive and corrective maintenance. These two strategies are polar opposites on the complete spectrum of asset management.
Those umbrellas can be broken down further into several subcategories, as explained by Road to Reliability.
- Time-based
- Failure-finding
- Condition-based
- Predictive
- Risk-based
Corrective maintenance
- Emergency (also known as reactive maintenance)
- Deferred
Before we dive deeper into their many subcategories, it’s imperative first to understand what each umbrella term is all about.
Preventive maintenance (PM) — as the name suggests — is all about stopping asset failure before it happens. Otherwise known as proactive maintenance, this strategy encompasses any and all maintenance tasks designed to ensure equipment performs primary functions as reliably as possible. Quite simply, PM navigates away from disruptions like equipment failure or unplanned downtime.
Corrective maintenance, in contrast, takes a reactive approach to asset management. Rather than strategize around avoiding or preventing asset failure, organizations that adopt this model prefer to address those disruptions after the fact. Simply put, equipment isn’t serviced until after it has failed. At that point, corrective maintenance becomes a race to reduce downtime (and the resulting production losses) as quickly as possible.
Although each strategy has its merits, neither is without downfall. Most often, organizations implement a combination of the two. But to do that, of course, you’ll need to know the ins and outs of their subcategories. Let’s take a closer look at specific preventive maintenance strategies:
- Time-based maintenance: This strategy refers to when maintenance personnel make repairs or restorations at a fixed interval of time. In essence, they schedule their maintenance tasks in advance of them breaking down.
- Failure-finding maintenance: In such a strategy, maintenance tasks are designed to detect a failure in protective assets rather than critical assets. Although it sounds meta, it’s really quite simple: Protective equipment is only used in the event that critical assets have already failed, so it’s important to know they’re working before they’re actually needed. In simpler terms, it’s a fail-safe system.
- Condition-based: Through condition monitoring, a facility can decide which equipment needs maintenance and which are operating sufficiently. This strategy is about grading the health of critical assets to determine if restorations are needed, whether it be in the long or short term.
- Predictive: As an extension of condition-based, predictive maintenance uses smart technologies — artificial intelligence and machine learning — to forecast asset failure. IoT sensors collect performance data to determine whether equipment failure is imminent and when maintenance is most optimal.
- Risk-based: This strategy assigns maintenance tasks based on risk assessment. Essentially, assets that carry the most risk are the most in need of repair at more frequent intervals.
By comparison, corrective (or reactive) maintenance strategies can be broken down as follows:
- Emergency maintenance: When the most critical assets fail out of the blue, maintenance personnel scrambles to mend the equipment. This strategy refers to the urgent and frantic nature of reactive maintenance.
- Deferred: Rather than react to equipment failure as needed, this strategy postpones maintenance activity for a later date.
Now that we know about each strategy, let’s dive deeper into what preventive and corrective maintenance have to offer.
Advantages and disadvantages of corrective and preventive maintenance
Firstly, it must be made clear that there’s no “one size fits all” approach to asset management. But to effectively decide which path — or more likely, a combination of paths — that your organization should take, you’ll need to examine the pros and cons of each.
In comparison to most preventive strategies, corrective maintenance can be less expensive in the short term. This is especially true for equipment with a low risk of asset failure or in industries where assets are easily replaced. It simply isn’t worth spending your time and resources on preventive action in those circumstances. Deferred maintenance, for example, postpones repairs to save costs in the short term, whether for budgetary reasons or because the asset is low-priority.
However, corrective maintenance can also be much more disruptive to critical business operations. In situations where critical assets do fail, production is upended by unplanned downtime and thrown for a tailspin. The resulting inefficiencies and losses may cost the company more in the long run, despite the short-term cost-benefit. By extension, emergency maintenance strategies can eventually become the most costly, because sudden disruptions leave maintenance personnel scrambling to repair or replace equipment and stop the bleeding.
In contrast, preventive maintenance strategies typically lengthen equipment life cycles. In turn, that longevity saves the company plenty of time and resources that would otherwise be spent replacing critical assets. Better yet, a proactive maintenance operation affords personnel a more organized, collected approach to asset restoration.
Most preventive measures, like time, risk or condition-based maintenance, reduce the frequency and/or likelihood of asset failure. Better yet, according to Deloitte, predictive maintenance increases productivity by 25%, reduces breakdowns by 70% and lowers maintenance cost by 25%.
However, preventive action is often much more expensive upfront. Plus, per IBM, 89% of asset failure occurs at random, no matter the equipment’s condition.
Choosing the ideal maintenance strategy for your equipment and employees
Every strategy has its pros and cons. That being said, employing an effective maintenance strategy is still an integral part of any facility’s operations.
Indeed, choosing the right strategy comes down to the particulars of your organization. More likely than not, preventive maintenance is the best option. For facilities with tighter budgets or fewer safety risks, corrective maintenance may make more sense.
Equipment maintenance, however, doesn’t exist on a binary; the most effective solution will be made up of many pieces. By combining strategies, you may most effectively identify your ideal maintenance strategy.
Leveraging technology for greater reliability in maintenance operations
No matter which approach you land on, any organization stands to benefit from technology. Tools like enterprise asset management (EAM) or computerized maintenance management systems (CMMS) platforms provide solutions that can help you realize your vision for efficient equipment maintenance.
Even for complex frameworks, like condition-based maintenance, EAM and CMMS software simplify the decision-making process. Dynaway’s Microsoft Dynamics 365-based platform allows you to take data from key ERP modules into consideration when executing your maintenance operation. In turn, you’ll be empowered to make better decisions, streamline maintenance tasks and ensure critical assets and employees are always at their safest.
Dynaway’s enterprise asset solution can bring greater intelligence to your maintenance operations. To learn more, check out our comprehensive EAM tool today.