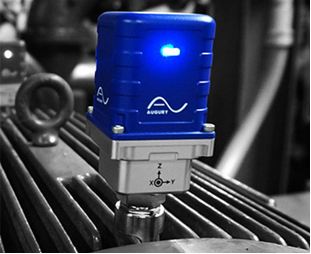
While it might not be precisely accurate to describe the current moment for the global economy as being "at a crossroads," it's certainly true that we're at a key point as we round the bend of 2021's first few months. Actions taken and processes put into place now will have a significant impact in the long term.
This is especially true in the various manufacturing and heavy industrial sectors: The latest report from the Institute for Supply Management (ISM) on the Manufacturing Purchasing Managers' Index (PMI) has noted manufacturing growth for 10 consecutive months as of March 2021 and indicated that new orders and production are on the rise. However, suppliers are not quite meeting customer demand. This could push them to overburden production equipment in the rush to produce and deliver goods more quickly. That, in turn, could put unusual stress on your assets that can ultimately increase the likelihood of equipment failure (or, at the very least, unplanned downtime, stemming from the need for impromptu repair).
Tri-axial, Bluetooth vibration sensor. Source: https://www.augury.com/machine-health-solutions/
Taking all of this into account, it's fair to say there may be no better time than now for manufacturers and other industrial organizations to take a hard look at the maintenance processes they currently follow. If we understand asset health at any moment in time, then we can perform that most cost-effective form of maintenance — condition-based maintenance. At the dawn of the industrial internet of things (IIoT), many asset-intensive and excellence-focused manufacturers are realizing the benefits of condition-based maintenance, such as the reduction of operational expenditure, improvement of output and increased asset health and knowledge through dynamic data.
Below, we'll look at the primary tenets of condition-based maintenance, and also more closely examine its primacy over other forms of maintenance strategy and its ever-growing relevance in the IIoT era.
What is Condition-Based Maintenance?
Understanding condition-based maintenance for key equipment
In simplistic terms, the diagram below shows how maintenance types are categorized. Preventive maintenance (sometimes called proactive maintenance) is divided into time-based maintenance and condition-based maintenance.
In a nutshell, condition-based maintenance entails performing a repair or replacement task based solely on the measured condition or health of any critical asset. At this stage, the component or machine in question has not failed, and it may not even be actively malfunctioning in any significant way.
The purpose of condition-based maintenance is to look for early warning signals of the potential or impending failure of an asset or component. You measure a specific parameter of an asset’s health such as vibration, temperature, or contamination. Then you trend the parameter value over time. When you believe it has reached a critical point that the asset is advancing towards a functional failure, then you schedule a condition-based maintenance intervention.
Some of the most well-known condition-based monitoring technologies include:
- Vibration analysis: Monitoring vibration levels and searching for patterns in the signals, often for machines with rotating components. Key performance indicators measured in this form of analysis include root-mean-square (RMS), standard deviation, kurtosis, peak amplitude and skewness.
- Infrared thermography: Detecting heat wavelengths to look for any abnormalities (excessive or insufficient heat, et. al.).
- Oil analysis: Used on any oil-lubricated machine to measure its viscosity, the presence of any contaminants or signs of the equipment's internal degradation.
- Ultrasound: Ideal for detecting the location of leaks in pressure and vacuum systems (boilers, heat exchangers, condensers and so on) and testing for arcing and corona in electrical components. Ultrasound sensors can also be employed to test the quality of machine lubricant and the functionality of gears, bearings, pumps, motors, steam traps, valves and many other components.
- Motor current signature analysis: Monitoring the magnitude of current wavelengths helps find key mechanical faults in equipment motors.
Online oil condition sensor. Source: https://oilqualitysensor.eu/ocm-on-generatorsets/
All of these repairs or machine health checks (and the various others that make up the common practice of CBM) are carried out well before an asset has failed or exhibited the potential for problems. This is also true of time-based maintenance, but unlike its conditional counterpart, TBM operations are conducted according to a fixed schedule.
Typical CBM maintenance interventions may include but are not limited to:
- Re-greasing bearings
- Tightening loose hold down bolts
- Balancing couplings
- Renewing electrical cable terminations
- Replacing a rolling element bearing
- Aligning pump sets
CBM at the forefront of equipment maintenance
When you are trying to establish the most appropriate maintenance strategy for your organization, it will be of the utmost importance to think from both a macro and a micro perspective before you actually put any program into place (let alone begin any actual nuts-and-bolts maintenance work). As you look at various machines, components or other assets, ask yourself point blank: "Is the asset or component I'm about to replace perfectly fine to continue operating?"
You often won't know the answer to this question until you pull the machine apart as much as is necessary for you to examine a given asset. Everything from a simple visual inspection to the various analysis methods mentioned above can be helpful in this context. Often as not, you'll find that the component you're scrutinizing is in good condition and perfectly safe to continue operating. Doing this manually is time-consuming, but with modern CBM, much of the monitoring is done through IIoT-enabled sensors that monitor all essential asset data in real time and can present key findings as organized reports in a matter of seconds. This is why condition-based maintenance is so cost-effective.
Time-based maintenance, while certainly better in most situations than a reactive strategy — in which you only repair or replace after partial or catastrophic failure of an asset — is often inferior to its CBM counterpart because of how regimented it is. If the intervals at which preventive maintenance is conducted are inflexible, you run the risk of effectively "over-maintaining" your assets. Regardless of the stability this framework may provide, it can easily become an excessive use of human and financial resources, which is why time-based maintenance is, not infrequently, more expensive to deploy than condition-based maintenance. In the final analysis, the latter stands out as the best choice for any organization looking to implement a strong framework of preventive maintenance.
The importance of CBM in the Industry 4.0 era of data analytics
In this new era of digital transformation and connectivity, diagnostic and analytical information is often available in real time to all stakeholders in asset information systems. This digital leverage greatly improves the planning and scheduling of maintenance. In turn, that can quickly lead to efficiency and effectiveness gains that help build the bottom line for modern, excellence-focused organizations.
With the arrival of permanently fitted sensors on our physical assets, the IIoT (or Industry 4.0, if you prefer) is changing the way we look at maintenance. You can think of it almost as "maintenance 4.0." Whichever of these terms you choose to use, one thing unites them: They represent nothing short of a revolution that is unfolding before our very eyes in the arena of industrial equipment maintenance. We're seeing a change from the old, inefficient methods to the new continuous and digitized monitoring of asset health and condition, with information dynamically delivered to the cloud via Bluetooth connections, Wi-Fi and gateways.
Given the context of increasing digitization in the manufacturing sector — along with most other broad categories of industry that make up the global economy — CBM is the most cost-effective and economical way of maintaining assets based on ongoing examination of an asset's actual deterioration (or lack thereof). It's certainly fair to note that CBM will have the highest monitoring costs, especially when compared to reactive maintenance, but it will also allow your organization to enjoy much lower asset repair costs and less unscheduled downtime than those you would see with either reactive maintenance or time-based maintenance. (Also, as IIoT technologies progressively advance, your monitoring expenditures will ultimately become negligible when examined next to the savings you'll see in other areas.)
Other advantages realized through CBM in the context of its connection to the IIoT include:
- Increased production output: If you can conduct real-time condition analysis and quickly spot any troubling patterns, you'll be able to plan and schedule maintenance more effectively. In the long run, this means your asset availability and performance levels will be higher — which can easily manifest as a notable uptick in production output.
- Longer asset life cycles: A reactionary maintenance strategy can be detrimental not only to individual assets that fail and necessitate emergency repair or replacement, but also to the many components to which the malfunctioning asset is connected. Sudden failures are stressful on any system. You may soon find yourself fixing not one component but several — or perhaps even an entire set of interconnected machines. CBM strategies that allow ongoing equipment monitoring extend the life cycles of your assets, potentially facilitating reductions in operational and capital expenditures.
- Improved planning, scheduling and spares forecasting: When you're in control of your asset maintenance — and not the other way around — you can carefully plan and schedule the allocation and deployment of your resources. Not only can you plan and forecast your spares well in advance, but also anticipate your human resource levels and plan accordingly.
- Reliability improvement: The ability to use condition monitoring and asset health information for defect elimination and various root-cause analysis processes is another one of its great benefits. CBM cannot improve asset reliability directly, but the information gained can later be used to improve the probability of successful mission time. When used in conjunction with a reliability program, the information you gain on our pumps, motors, fans, gearboxes and various other components is invaluable for reducing the likelihood of defects and asset failures in the future.
Implementing CBM with sensors and asset monitoring software
In a CBM framework facilitated by the IIoT, data is constantly streaming back to the cloud and then through IIoT value chains, driving the performance of the predictive maintenance strategy higher and higher. This ultimately serves to transform and bolster the maintenance programs of the companies that strive for excellence by employing the most cutting-edge business intelligence and real-time data analysis in the context of their physical asset condition management strategies.
Advanced IoT sensors are critical for the most effective deployment of a CBM initiative. The path from a sensor's detection of a potential problem to proper intervention through maintenance (or repair) can be short and sharp: IoT sensor data can be used to trigger work orders directly from your computerized management maintenance system (CMMS) or enterprise asset management (EAM) platform.
By turning to Dynaway for your EAM needs, you can gain even more control over your maintenance operation: Our solution can operate seamlessly alongside Microsoft Dynamics 365 or with Microsoft Dynamics AX2012. Also, while Dynaway is primarily operated as part of the cloud-based Dynamics 365, we can implement an on-premises deployment of Dynaway EAM. We are the undisputed progenitor of modern EAM, offering a comprehensive approach to the thorny issues of asset oversight that's critical for an increasingly unpredictable market.
This is how the maintenance landscape is changing: Industry 4.0 is growing and infusing everything you see around you. Faults are being discovered faster and faster. The risks of unplanned downtime are lowering every moment that passes. Condition based maintenance is well-placed to take advantage of the value that can be delivered through digital transformation in the industrial arena.
You can bring greater intelligence and comprehensive oversight to your maintenance processes by leveraging the full spectrum of Dynaway EAM's possibilities.