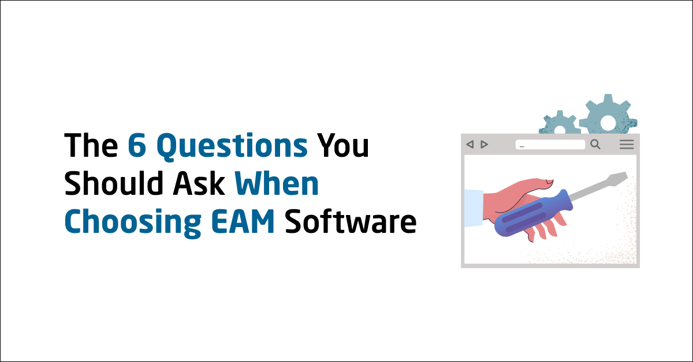
It’s tough choosing the right maintenance management software.
And it’s a big deal because it will be the pumping heart of your maintenance and work management system. A good one will regulate, monitor, control, and keep the whole process running optimally.
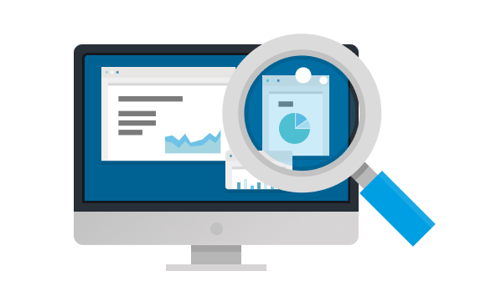
It can be daunting when you start looking at the market out there. There are stacks of options, tons of features, reams of marketing pages, and even webinars (and articles like this one) to keep you awake at night. And you know what? If you’re a maintenance or engineering manager these days, you just haven’t got the time to get through all the marketing and Zoom calls.
Then how can you get to choose the right one for your organization a bit quicker?
Ask yourself these questions that will get to the core of your problems in your organization.
1. Do we really know what we want?
Salespeople and service providers will be smiling at this one.
Don’t be that maintenance manager that asks a consultant, ‘We need to improve OEE. Can you just do some asset management to our plant?’.
You will get to an optimum solution much quicker if you understand the deficiencies of your own maintenance systems, processes, and current practices. Audit yourself against best practices. Develop your specific requirements. Do you know what your pain points are with your existing software? How is it ineffective or inefficient? Or, if you’re still using Excel or even paper and pencil, then use the pencil to draw up a scope or requirements plan that brings you into the modern-day.
Just don’t go to the EAM/CMMS vendor and say: ‘We’ve got a budget. Give us something to manage our maintenance’. You’re asking for pain.
2. Does it do the stuff we want it to?
Simple.
After question 1, if you now know what you want, then go start the serious talk with a couple of vendors. Be aware! You’re more likely to find the everlasting rolling element bearing than the perfect EAM/CMMS solution – but you will get close if you do your homework.
If your focus is on asset and work management, reliability, and availability, then find out if it does want you want it to do:
- Asset Registers
- Spares & Vendor Management
- Planning & Scheduling
- Work Requests / Orders
- Work Order Failure Codes
- KPIs
- Bad Actor reporting
- Automated Alerts
- Mobile Device App
3. Are we mature enough to get the best out of it?
This is an important one. Self-reflect a little. It can be painful but be honest.
Maintenance departments worldwide cover the whole spectrum of maturity: from the very immature laggards to the highly advanced. If you were to do a self-audit, would you find that there are significant gaps in your team’s competencies and capabilities? Not just failings in maintenance execution, but in understanding work management processes, the importance of work orders or even how to use a PC and keyboard. Then if so, you’ll need to budget for upskilling and engagement in these, not just the software purchase.
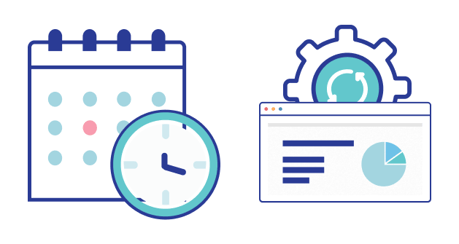
And not only that.
What about your internal processes for reliability improvement, work management and planning and scheduling? If these are at an immature level or non-existent, then no EAM or CMMS can magically improve them. Strategies, frameworks, and common understanding need to be in place. The software is not a magic wand.
4. Is it actually any good?
Now we are getting to the delicate part.
There are lots of providers out there. There’s us at Dynaway, but there’s also Fiix, Limble, Upkeep, eMaint, AssetCloud, Infraspeak, Asset Panda, SAP, IBM Maximo, Shire, and many others. But you need to know if the software is any good in practice.
Was it designed by people who’ve never worked a night shift maintaining a boiler room or who have never withstood the daily pressures of maintenance management?
Probably not, but that doesn’t mean it won’t be able to deliver value to you. At Dynaway, for example, we believe in two-way trust. If we can’t deliver something, we’ll be honest and we’ll let you know that we can’t. That way, there are no nasty surprises later on.
So when it comes to your research, don’t just read the case studies on the website. Ask the vendor if you can speak to some of their existing clients. Most vendors would be happy to oblige if they are confident in the product. Everyone knows that all technologies have advantages and limitations - let’s be open and honest about the balance between the good and the bad.
When you get to speak to that existing client, ask them:
- What’s the best thing about it?
- What irritates you and your team about it?
- What improvements have you seen since you started using it?
- Is it really value for money?
- What’s the customer service like?
And get your maintenance team involved in this conversation. That’s mandatory.
5. Is the vendor willing to listen if we think it could do better?
Nowadays, this is critical.
You will find elements of any software that slow you down or restrict you. So, why not ask the vendor if they often make improvements based on reasonable client requests?
It’s only a bit of code, right?
Some EAM/CMMS providers can be slow to react to customer requests. And this is understandable when faced with significant software code and processes that most customers may be happy with. Then there are other EAM/CMMS systems that may be quicker when it comes to making software improvements and upgrades. And often they are free!
6. How painful will our headache be when it comes to integrating and implementing it?
Let’s be honest. Integration can be horrendous if not managed adequately. Think in terms of:
- Data and Information – are the existing asset register, spares, and PMs accurate? Will you plan properly for the migration?
- Business Continuity – how long will the migration and transition take? How will maintenance be managed in the meantime? What if stuff gets lost?
- System Integration - Do data structures and tables match up? Will the software communicate easily with others? Have we got the IT people to manage this?
- Organizational Acceptance – is your team accepting of change? Will you manage the communications adequately? Will you show them what’s in it for them? As Peter Drucker once said, ‘Culture eats strategy for breakfast’.
Purchase Right, Manage the Change
No matter how big or small your organization, choose the right software. And remember, the change has to be managed – stakeholders, plans, communication, risk register, and all the rest. Don’t be that maintenance manager that regrets the purchase six months later. Are you ready for all of the above?
It’s going to hurt a little.
Maybe a lot.
But do it right, and your team and organization will reap the rewards for years to come.