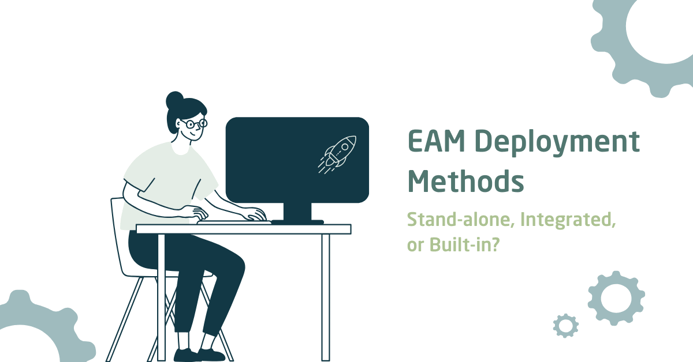
The need to be a good administrator of assets is not a new concept for businesses. For years, producers have invested in asset maintenance. This is essential to reduce downtime and costs; however, executing it is time-consuming.
Currently, many manufacturers are using disparate systems for this and other purposes. As we move towards the Factory of the Future, this siloed approach will become a relic in the “museum of manufacturing business processes past.” Companies that want to remain competitive are already looking for ways to streamline Enterprise Asset Management (EAM) processes with other systems, such as Enterprise Resource Planning (ERP).
Let’s explore the current state of EAM and examine how a modern EAM solution can play a pivotal role in the digital transformation of manufacturing organizations.
EAM System Integration
More systems, more problems
Systems like EAM and ERP exist separately in many manufacturing organizations today, and it’s not uncommon for different departments, such as production and maintenance, to maintain their databases with job information.
Read more: https://www.dynaway.com/customer-stories/-grande-cheese-24/7-production
While manufacturers can function using disparate systems, this fragmented approach has various downstream effects. When processes aren’t integrated, teams are likely to duplicate efforts, and data entry is likely to be completed manually, which is inefficient. ARC estimates from 2016 state that only 23% of issues identified by predictive maintenance systems are automatically integrated into business processes—meaning there’s still an opportunity for more than 75% of these integration efforts to be automated¹.
Disparate systems also prevent teams from having a line of sight into each other’s planning processes, make it difficult to generate reports and gather business intelligence, and lead to “shadow inventory,” which inflates working capital. It’s estimated that 43% of excess working capital can be traced back to inventory².
Ideally, the information would flow freely, and these systems and processes would interoperate to improve efficiency, provide visibility across roles and departments, enable effective reporting, and give manufacturers better control over inventory management. What’s needed is an approach that addresses challenges while providing the right capabilities for each role in the organization.
Deployment Method Matters
Stand-alone EAM Deployment
As it presently stands, there are multiple ways to deploy an EAM solution. Companies may choose to implement stand-alone solutions, such as Limble CMMS, UpKeep, Fiix, Hippo CMMS, or eMaint, which deploy quickly but don’t solve for data silos.
Most manufacturers choose to implement third-party solutions that are later “bolted onto” their ERP systems. These third-party solutions often include robust feature sets. Still, the number of features makes for a complex data integration effort and has the potential to overwhelm the employees who must use them in the end.
Integrated EAM Deployment
The ideal scenario, however, is to build the EAM system on a foundation of intelligence, which is achievable by fully integrating the EAM with other business systems such as ERP.
A built-in approach streamlines disparate systems and enables manufacturers to reduce duplicate efforts, gain better visibility across the organization, improve their capacity to generate reports, and manage inventory more effectively.
Built-in EAM Deployment
Equally as crucial to a modern EAM approach is a human-centric focus.
Today’s manufacturing workforce is, on average, younger and more tech-savvy than in recent years, and any new EAM system should meet its collective needs. A solution with a user-friendly mobile client that surfaces the information employees need, when they need it, meets this need without overwhelming employees with information.
While addressing these day-to-day needs may seem trivial, their long-term ramifications are invaluable to a modern business’s ability to gain tighter control over maintenance planning and better procedures for documenting organizational outputs. In doing so, manufacturers can reduce the amount of effort and revenue wrapped up in preventing downtime and dedicate more to activities that enable revenue growth.
EAM Built Right Into Your ERP
Dynaway EAM, built on Microsoft Cloud technology, is a modern asset management solution that enables manufacturers to achieve operational excellence by improving machine effectiveness, reducing the administrative burden, and controlling organizational costs.
Unlike stand-alone or bolted-on 3rd party solutions, Dynaway EAM is built into Microsoft Dynamics 365 (Business Central and Finance & Supply Chain Management).
This approach unifies the ERP and EAM functions of a business, benefitting manufacturers by streamlining information that was once siloed and providing real-time visibility across the organization.
1ARC, Enterprise Asset Management Global Market Research Study, 2016
2Digitalist Magazine, Optimizing Working Capital Through Better Inventory Management, 2013