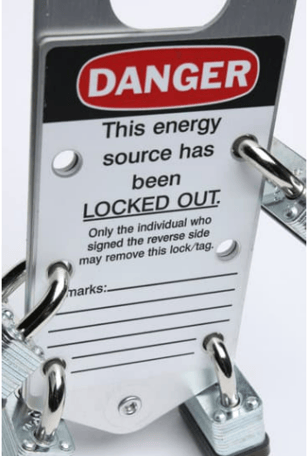
In the first installment of this two-part blog series, we provided a basic overview of the lockout tagout procedure (sometimes simply called LOTO). This refers to the essential processes for disabling and powering down any equipment that is scheduled for a maintenance operation, preventing other employees from accessing it and identifying its "locked" status with clearly visible tags.
For this chapter, we will delve more deeply into the specific steps involved in lockout tagout, including those pertaining to certain types of facility hazards that can be particularly hazardous to workers' health and safety. We will see that a consistently effective LOTO procedure — implemented in compliance with government standards and continuously followed by all staff — will contribute significantly to a safer workplace.
The critical importance of lockout tagout
No one, if asked, would deny that workplace safety is important. But it is also impossible to deny that LOTO is not always treated with the level of importance that it should. Data from recent years bears this out:
- In the 2020 fiscal year, violations of lockout tagout regulations ranked No. 6 on the U.S. Occupational Safety and Health Administration (OSHA) list of the 10 most frequently cited standards, issuing 2,065 violations for that period.
- That was the first year in quite a while that OSHA's LOTO standard (147) was not one of the top five most frequently cited standards. For the past six consecutive years, the regulation had reached the top five — e.g., in 2019, it reached No. 4, and for 2018 it had been No. 5.
- According to data retrieved from the OSHA website Oct. 7, 2021, the agency had conducted 709 inspections based on suspicion of LOTO violations and issued more than 1,300 violations (which led to over $8 million in penalties) between October 2020 and September 2021.
- By contrast, the EU does not issue regular reports on violations of its LOTO standards (89/655 and EN 1037). But in the most recent European Survey of Enterprises on New and Emerging Risks (ESENER) conducted by the European Agency for Safety and Health at Work (EU-OSHA), "risk of accidents with machines" and "risk of accidents with vehicles in the course of work" were cited as notable risk factors in over 40% of European work establishments.
The financial penalties that result from failing to meet government-mandated LOTO procedure guidelines are far from the only adverse consequences of such compliance lapses. Accidents that occur due to the release of hazardous energy could destroy equipment and damage the facility. Also, serious injuries or deaths of workers could also lead to civil lawsuits, reputational damage and possibly even criminal liability.
Anatomy of the LOTO procedure
Conducting an effective lockout and tagout for a particular machine, device or system requires the creation of detailed procedures for each class of equipment. These would usually detail the steps for powering down, deactivating and restarting, as well as information regarding all energy sources to which the equipment is connected.
You also designate who plays the role of "authorized employee" in the LOTO process. This can be anyone on the maintenance team who is qualified to perform maintenance on various types of industrial equipment. Ideally, they have experience dealing with whatever hazards may be involved: electrical energy, extreme heat, volatile chemicals and the various types of hazardous energy release (pressure overflow, gas leaks and so on). Only an authorized worker, designated as such in your LOTO program guidelines, should be allowed to attach a lockout device to a machine, trigger any virtual lockout process (if applicable) or affix a tag.
Everyone else who works with the equipment that's about to undergo maintenance activity or whose duties will be interrupted by the maintenance downtime is considered an affected employee (AFE). All AFEs should be notified of the forthcoming lockout well in advance of lockdown and told how long maintenance is likely to take. Once everyone is informed, the authorized employee will then put in a request for a work permit, which should specify the type of hazard the job will entail (hot, mechanical, electrical, crane usage, line breaks and so on).
Then, the machine is shut down and disconnected from any energy source (primary or secondary) it uses. An isolating device or disconnect switch will be engaged to ensure the equipment stays deactivated and doesn't experience unexpected energization. Either of these could constitute the "lock" of this particular lockout, but not necessarily; physical locks or virtual lockout procedures may also be used.
Maintenance work can now begin. If shift changes of any kind take place while the equipment is still being serviced, the incoming workers should be informed in advance. After maintenance is complete, an authorized employee can remove the locks and tags and the machine can go back online.
Best practices and tools for improved safety through LOTO
Policies with precise details on how every relevant class of equipment should be locked and tagged out are the heart of any LOTO safety framework. Each LOTO policy should be easily accessible to employees and followed to the letter, using the OSHA standard for LOTO (and other pertinent regulations) as a baseline.
To maintain awareness and ability, all employees are periodically trained and re-trained in any LOTO procedures relevant to their jobs. Even those who will generally be AFEs during maintenance operations must know what should be done to avoid interfering with repair and upkeep. Additionally, the maintenance department should audit its LOTO practices at least once a year to ensure they remain relevant and adjust as needed. Last but not least, it's best to exercise an overabundance of caution:. This includes everything from assigning veteran workers to supervise team members who have only recently become authorized employees to ensuring the availability of tools, spare parts and relevant personal protective equipment (PPE).
Give yourself full visibility and control of LOTO with the Dynaway Safe Work module, which readily integrates with Microsoft Dynamics 365 Finance and Operations Asset Management.