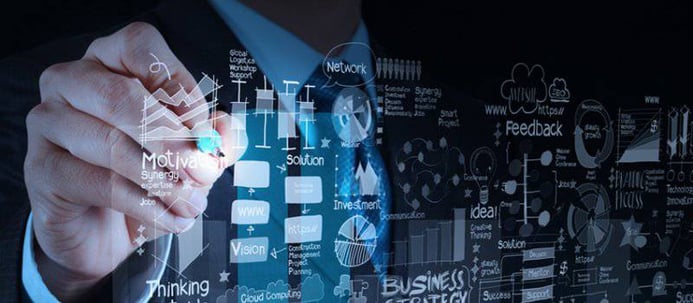
Maintenance is changing. Rapidly.
Predictive maintenance is evolving almost by the hour.
Just like the rest of the world, maintenance is becoming connected and interconnected all at once. Sensors are spreading far and wide across the industrial landscape at a searing pace.
Volts, amps, and zeroes and ones stream back and forth through millions and trillions of cables and wireless connections - delivering data, information, and value to modern organizations that demand operational excellence.
The internet of things (IoT) has now industrialized (IIoT) and is driving the 4th industrial revolution – industry 4.0 – before our very eyes.
Internet of Things is a vision where every object in the world has the potential to connect to the internet and provide their data so as to derive actionable insights on its own or through other connected objects. Enterprise IoT: A Definitive Handbook by N. Balani |
Traditional maintenance is evolving into informed, data-driven, digital, and dynamic strategies where intelligent decisions are made on asset health and performance – not just guess work, assumptions, or vendor recommendations.
The critical asset data are sent to machine learning algorithms, predictive models, and cloud-based software, which automate the intelligent decision-making process and which, ultimately, improves your chances of high asset reliability and availability.
And IoT sensors are key to that intelligence.
Maintenance intelligence is within your organization’s reach.
Where do you start with IIoT?
Whether you are a small manufacturer of a popular craft beer or a multi-national petrochemical plant, IoT sensors and predictive maintenance (PdM) are now accessible. They are no longer the preserve of large, global, cash-rich corporations.
The hardware and software are affordable and accessible to all.
If you are an asset-intensive organization that seeks intelligent decision-making and real-time data analysis, then start that journey to predictive maintenance. The competitive advantage will be yours. McKinsey* states that by 2025, the positive economic impact of IoT on US factories will be between $1.2 and $3.7 trillion dollars.
And that’s hard to ignore.
The steady rise of ‘predictive maintenance’ in Google Trends.
Predictive maintenance – also known as condition monitoring – has certain key techniques and technologies that enable real-time analysis of asset health and condition. They can detect and diagnose impending asset and equipment issues for your organization, providing actionable insights and a prognosis on the remaining useful life of the system, asset, or component.
And you know what it means?
You’ve got it!
The central objectives of value-delivery in asset management: reduce organizational risks and costs and increase asset performance.
The Key IoT Predictive Maintenance Technologies and Sensors
There are 5 key technologies in predictive maintenance.
While these proactive technologies have different types of sensors and real-time monitoring devices, they all lend themselves to the IIoT and Industry 4.0 and the inevitable march towards a digital and interconnected world.
Vibration Analysis
This technology is the best all-rounder. It covers a lot of potential asset issues and is best suited to rotating equipment.
You’ve probably got a lot of those, right?
It’s a mature PdM technology that uses an accelerometer sensor to measure an asset’s vibration levels. The sensor can send signals back to servers via hard-wired cables, or wirelessly via cellular networks or Wi-Fi.
The severity of the vibration is trended and can change over time.
When vibration levels increase and breach pre-set alarm levels, this often indicates asset or component deterioration.
And serious consequences can follow without maintenance intervention.
Common defects that can be detected with vibration analysis include:
- Unbalance
- Misalignment
- Resonance
- Bearing wear
- Gear teeth damage
- Cavitation
But the full list can be extensive.
Source: www.emerson.com
This initial phase is the detection phase. It’s all about getting an early warning from the technology. Software algorithms will then help identify the specific failure mode as each will have its own unique vibration signature or frequency – this is the diagnose phase. Predictive models will then aid in the prognosis phase. This is to determine the remaining useful life of the component.
Infrared Thermography
Thermal imaging takes advantage of advanced camera electronics to ‘see’ and measure the longer wavelengths of the electromagnetic spectrum. This is where we can ‘see’ heat or thermal energy that is being emitted from any type of object. In your organization, this could be a pump, motor, vessel, boiler, building, tank, engine, or anything!
Changes in temperature are often a particularly good indicator of impending failure or a failing process.
Infrared thermography can detect a range of issues and failure modes. These may include:
- Electrical cable / insulation failures
- Loose electrical connections & joints
- Gas escape
- Unbalanced loads
- Overheating manifolds
- Damaged or missing insulation
- Worn refractories
- Worn bearings
- Coupling misalignment
Source: www.novatestpro.com
Though it was once an expensive PdM option, it is now affordable, smaller, and easier to use. Connectivity to the IIoT is now easy to achieve along with the constant, online monitoring of a range of industrial systems and assets.
Oil Analysis
As well as being used for grease, this PdM technology is mainly utilized for assessing lubricating oil fluid condition, external contaminants, and internal component wear particles.
Lubricants are the life blood of rotating assets, and when the blood goes bad… the asset won’t be far behind.
Source: www.ph.parker.com
Oil analysis can highlight many failure modes, including the following:
- Worn bearings
- Gear teeth damage
- Depleted lubricant additives
- Low oil viscosity
- Fuel ingress
- Varnishing
- Dirt ingress
- Water contamination
There are several types of online oil analysis sensors that your organization can use when developing its IoT approach. These include oil health sensors, visible-near infrared sensors, and optical particle detectors.
Remember, oil is the life blood.
Look after it.
Motor Current Signature Analysis
MCSA is primarily focused on monitoring the health and condition of AC induction motors.
But given that these assets are so abundant and ubiquitous in all industries, there is inherent value in assuring their reliability and availability.
If they don’t turn, then the wheels of industry don’t turn.
For engineers, the recognition of motor current fault signatures would require a considerable degree of expertise and experience, but modern MCSA tools take care of that. The online system delivers an automated interpretation using powerful artificial intelligence algorithms that detect and diagnose imminent failure in AC induction motors and pumps. www.semioticlabs.com |
MCSA utilizes motor current (and voltage) measurements to detect a range of failure modes or faults in the supply voltage, and motor components such as the stator, rotor, and terminal box.
Source: www.signaguard.com
Ultrasound
This technology can detect airborne and structure-borne ultrasound emissions. These are non-audible to humans and are commonly found above 20kHz in frequency. Thanks to advanced electronics, these sounds can be heterodyned and made audible to humans and allows us to hear mechanical friction, turbulence, and impacts.
Ultrasound has a range of applications and can detect many failure modes, including:
- Electrical corona & arcing
- Leak detection
- Faulty valves
- Electrical contact chattering
- Worn bearings
- Gear teeth defects
- Lack of lubrication
- Faulty steam traps
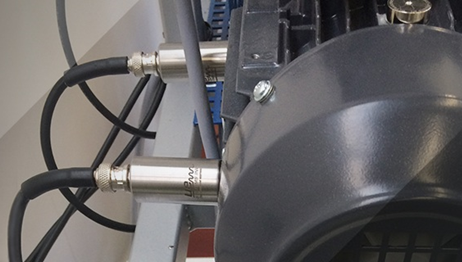
Source: www.uesystems.com
It is very well suited for early stage fault detection in rolling element bearings.
In terms of IIoT applications in industry, the most common ultrasound sensors are used for detecting structure-borne defects. This means they are most often used to detect common bearing problems: damaged raceways, defective balls or rollers, lack of lubrication, and fatigue.
This overview of the key IIoT predictive maintenance technologies and sensors has shown us that there are several options to give our organizations a competitive advantage in a rapidly changing maintenance landscape.
If we want to make data-driven and intelligent decisions on our maintenance interventions, then we can do so!
Connectivity and the future of predictive maintenance is within our reach.
Read next: Comprehensive guide to IIoT in Maintenance