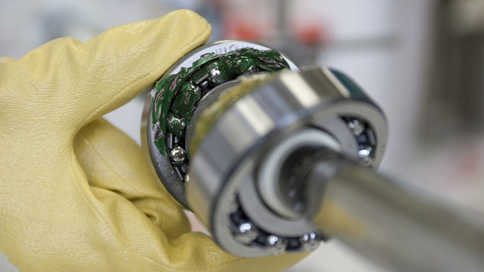
Lubrication.
That word makes some people smile.
But in industrial organizations world-wide, it gives most people a headache.
Why?
It’s very often a major contributor to rotating equipment failures and downtime. Whether it’s the wrong lubrication, too much lubrication, too little lubrication, contaminated lubrication, failed lubrication, or just ‘I don’t know!’ lubrication.
It can make grown men and women cry as they look at their availability KPIs go up in smoke every month. Bad practices can cripple your progress.
We’ll come back to that later.
First the basics.
What is lubrication?
It may sound like a simple thing, lubrication. When somethings squeaks, you squirt a bit of grease here and there. You may top up the oil occasionally as the manual tells you.
The fact is there is much more to it.
"Lubrication is the control of friction and wear by the introduction of a friction-reducing film between moving surfaces in contact. The lubricant used can be a fluid, solid, or plastic substance." Wes Cash, Noria Corporation. |
The act of lubrication itself is all about reducing friction and wear between moving surfaces - and you will have lots of those in your industrial equipment. Other than that, lubrication is also used to achieve several other critical equipment objectives:
- Cooling (heat dissipation)
- Cleaning (contaminant transport to filters)
- Corrosion reduction
- Shock absorption
- Sealing from contaminants
- Power transmission
Given this range of critical lubrication functions, what types of lubrication are available to us?
Lubricating oils and greases
Lubricants are the lifeblood of rotating equipment. Don’t ever forget that. And when the blood goes bad, the equipment won’t be far behind.
Lack of grease. Source: https://assetivo.com/
Never underestimate the importance of the lubricant.
"Bearings fail for many reasons, but improper lubrication is at the top of the list, according to a variety of studies:
Applied Industrial Technologies, machinerylubrication.com |
Broadly split, lubricants fall into two camps: lubricating oils and greases.
Lubricating Oils
Lubricating oils contain base oil stock (70 to 98%) and additives (2 to 30%). The base oil controls the properties of an oil and it is typically mineral or synthetic. Additives determine the oil’s performance characteristics and these are typically organic or inorganic. Here are some typical additives:
- Anti-oxidants – they stop oxygen reaction and reduce corrosion and sludge
- Detergents – counteract acids, and clean deposits and sludge
- Extreme pressure additives – creates a film that stops adhesive wear
Source: https://www.kematbelgium.com/application/lubricating-oils/
Lubricating Greases
Lubricating grease contains base oil stock (70 to 95%) and additives (0 to 10%), but also a thickener (3 to 30%). The thickener is the key difference with oil. The base oil - typically mineral or synthetic -controls the properties of the grease. Again, additives (organic or inorganic) determine the oil’s performance characteristics. The thickener consists of simple or complex metal soaps and non-soaps and its purpose is to thicken it all up.
Source: https://www.shell.com/business-customers/aviation/aeroshell/aeroshell-greases.html
That’s the rudimentary differences between the oils and greases.
But why and where are they used?
Oil and greases: the why and the where
Lubricating oils are particularly good at cooling applications – anywhere heat needs to be carried away. Think of your hot car engine block for example and the oil constantly being circulated. The same thing happens in industrial reciprocating compressors.
Oils are used to lubricate and cool industrial gearboxes and the high sliding and friction action that is generated between gear teeth. One advantage here – over grease - is that oil can carry contamination away (such as metal and dirt) to filters.
Source: https://www.plantservices.com/articles/2012/01-troubleshoot-pump-bearing-failures/
Oils are also great for light load, high speed applications and are often used for pump and turbine bearings. You will likely see oil bath, oil ring, or oil mist lubrication. And anywhere chain driven conveyors are employed, you’d probably see oil drip lubrication.
Greases, on the other hand, are used often where assets are in a high contaminant environment – it is good at sealing out external dust for example. Think of bearings in the steel industry. It is also often seen lubricating machines that operate intermittently such as automotive body presses. Grease handles starts and stops much better than oil.
Grease should always be the first choice for heavy static and dynamic loads on bearings, and particularly where there is slow rotation. When you see huge cranes slewing around in a circle, their bearings have been packed with grease using a grease gun.
Source: https://www.cargister.com/best-grease-gun-reviews/
Earlier we stated that 40-50% of bearing failures are caused by improper lubrication. Improper is a catch all term that relates to all the good, the bad and the ugly lubrication practices.
Let’s look into what they are?
Worst practices: Lubrication malpractice
For the sake of you and your boss’s health, wealth, and happiness, avoid these at all costs:
- Storing lubricating oil and grease outside in the wind, rain, sun, and snow
- Leaving the lids and caps off – open to the environment (moisture, dust, dirt, swarf)
- Dispensing multiple types of oil or grease with one canister or gun (cross contamination)
- Using dirty equipment to change or filter oil
- Over-greasing
- Under-greasing
- Accepting oil leaks or water in the oil as ‘business as usual’
- Willingly using the wrong lubricant for an application
You may hear unenlightened technicians cry, “but, grease is grease, it’ll be fine!” to defend using the wrong lubricant. But things will not be fine. If your blood group was ‘B’ you wouldn’t accept a transfusion of 5 liters of ‘A’, would you? You probably wouldn’t.
These were common bad practices in lubrication.
To make sure you get off on the right foot, what about best practices you can implement if you are new to the lubrication game?
Best practices: Lubrication excellence
- Lubricate assets with the right type, the right amount, and at the right frequency
- Keep oil and grease cool and dry – indoors and at ambient temperature
- Use ID tags on all lubrication dispensing equipment and asset points
- Reduce and consolidate lubricants
- Perform oil analysis on critical assets
- Clean and change oil filters at the right time
- Set up preventive maintenance lubrication tasks in your EAM
- Sample new lubricating oil deliveries
- Train lubrication technicians/engineers to at least MLA1
Of course, there many more best practices, but these are some of the most important.
Lubrication is critical and it deserves your highest attention. Remember the cause of 40 –50 percent of bearing failures? Well, that can be avoided if you pay attention. It is the true lifeblood of industrial machinery and assets and you should treat it as you would your own blood. Keep it fresh. Keep it cool. Sample it. Don’t let the lubricant leak out!
And don’t let the dust and dirt in.
Want to achieve high asset availability and reliability?
The way you do maintenance is evolving. Dynaway EAM for Business Central is a simple yet intuitive solution that is easy to use and helps you to bridge all the gaps in your Maintenance Planning.
Spend less time behind the computer and more time maintaining your assets!