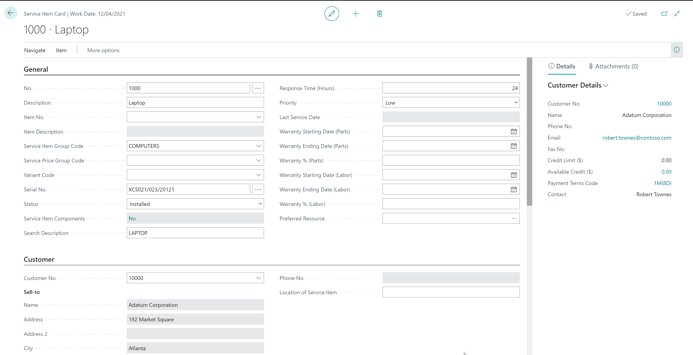
The Service Management module comes as standard functionality in Microsoft Dynamics 365 Business Central Premium Plan. This article explains what makes that Dynaway EAM functionality unique and outlines the benefits you would gain by using the EAM and other Dynaway applications.
Service Module Overview
The standard Service Management module has been developed for companies that sell items to their customers and then service the equipment if it breaks, and repairs are needed. Items sold through a Sales Order can be created as Service Items and attached to a specific Customer. The important aspect here is that the customer owns the item in most cases.
If anything breaks, the customer can call the company and raise the service order. The module also allows creating a service contract with a customer that enables the company to perform a preventive service order, for example, every x number of days and issue the invoice every month or year.
When does the EAM fit better to your business?
Compared to the standard Business Central module, the biggest difference is that Dynaway EAM focuses on internal equipment owned or leased by the company.
Maintaining assets in a manufacturing company requires much more detail than servicing items that have been sold. It requires continuous monitoring of the equipment. Some companies have more than 200.000 assets in their facility. This includes both high-level assets such as a production line and lower-level assets such as conveyor belts, robots, and specialized equipment on that production line. Therefore, in Dynaway EAM, it is possible to build a hierarchy of the assets - the asset tree. And plan, register, and track the maintenance on each level.
Looking from a cost perspective, the maintenance of the equipment in the company is also different than when doing the service. Questions that many ask are how much we spent on the maintenance of the equipment. Are we on a budget, or is it still worth maintaining the asset instead of buying the new one?
Financially, most of the assets are also listed as fixed assets in the company. This means a connection is needed between two worlds – finance and technology – to provide financial insights into maintenance costing. This is where Dynaway EAM can help, and the service module cannot be used. Further, each cost registered for the maintenance is marked with the fixed asset number.
When looking into maintenance planning, it is more complicated than doing service every single month or so. There are many variants to plan the preventive, but also reactive, maintenance.
With Dynaway EAM, you can track the data from your equipment and plan the maintenance. Such data can be based on counters (running hours or mileage), on IoT devices (pressure is too high, the temperature is too low, etc.). This allows you to plan needed resources and maintain the stock of the necessary spare parts for future work.
Service is not the same as maintenance
Choosing the right tool matters. There is a difference between maintenance and service. When selecting the module right for your company, you should consider the main business processes. Dynaway EAM fits better if it is important to control the life cycle of the assets and plan preventive maintenance. The standard service module fits if the asset life cycle is less critical - the assets are owned by the 3rd party and are mainly serviced ad-hoc or by a simple calendar-based contract with the customer.