Maintenance operations in any manufacturing or industrial facility always involve a great deal of moving parts — both literally and figuratively: Physical equipment, machinery, tools, spare parts, vehicles, plant infrastructure and personnel must all be managed carefully, to keep operational workflows on track, minimize downtime and facilitate efficient production.
In the modern world of facility management for manufacturing and heavy industry, where Industry 4.0 and the industrial internet of things (IIoT) are foundational tenets, maintenance management can only be accomplished by using some kind of work order software. But how do you know which work order management system is best for your organization's specific needs? Read on for an exploration of the background, essential features and potential benefits of these essential solutions.
Work order software: The fundamentals
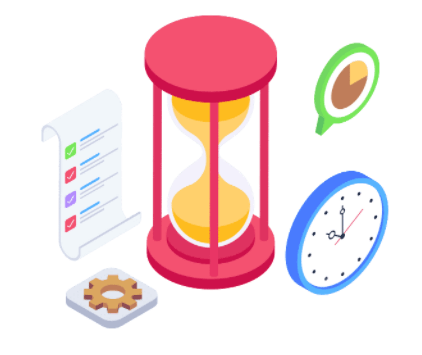
There is no one-size-fits-all definition that precisely describes all of the different variations of this software category.
That said, it's generally fair to characterize work order software as such: a solution that allows facility managers and other appropriate supervisors to track the creation, management, life cycle and archiving of every maintenance service request and work order. Any industry where physical infrastructure is integral to operations will benefit from a work order management software solution, so you commonly see these tools in oil and gas production, construction, transportation and power generation as well as manufacturing.
These solutions usually have a dashboard interface through which all essential work order tasks can be overseen and initiated. Much of the work order creation process is automated, so it's just a matter of a few clicks and keystrokes to get the ball rolling on a work request or order.
A brief history of work order software
The earliest solutions that aimed to serve the purposes of modern work order software began to emerge in the 1960s, according to American Machinist. These were the prototypical computerized maintenance management system (CMMS) tools, and served a purpose not dissimilar to what a CMMS does now, but in much more rudimentary fashion: The earliest iterations used punch cards fed into the computer using card readers, or required members of the maintenance team to fill out paper work orders that were then manually typed into a mainframe.
Once personal computers became commonly available and programming languages diversified beyond COBOL and Fortran, more varieties of work order software could be developed. The emergence of the internet — and, decades later, cloud computing — further revolutionized order management software. Most of the work order system tools you'll see today are available as software as a service (SaaS) applications hosted in the cloud; in fact, some are cloud-exclusive.
Types of work order software
There are many different types of work order management software available on the market today, but they typically fall into one of the following three categories:
- Basic order management software: These a la carte solutions strictly deal with the basic steps necessary to complete the work order life cycle: assign, track and record. While they are automated and can be useful to small or medium enterprises (SMEs) in any of the sectors detailed earlier in this article, the limitations of these solutions are hard to ignore.
- CMMS software: This type of work order software is much more multifaceted. Its chief advantage is the strength of its database. That foundation allows for comprehensive asset management through oversight into materials, parts, equipment and all other assets, in addition to everything needed to manage maintenance work orders. It can be helpful for establishing a viable preventive maintenance framework.
- Field service management (FSM) software: If a maintenance task requires you to send field technicians outside the facility, FSM solutions allow you to manage the work order process remotely. Techs can also use the FSM platform to communicate with other team members and deliver invoices to clients.
- Enterprise asset management (EAM) solutions: EAM can best be defined as an expansion of CMMS software. It serves all of the purposes of a CMMS tool but, critically, does so in the context of the larger business, through integration with purchase order modules and enterprise resource planning (ERP) systems.
Key features of a work order management solution
As we've established that the ideal work order software should allow you to do more than just assign and process work orders, you'll want to look for a solution that has a broad range of capabilities. The most essential features are as follows:
- Asset management: Proper oversight of your facility's assets is dependent on having ready access to key information about all of them. Asset management in order software should allow you to quickly learn an asset's location, find classifying details (model and serial numbers, etc.), read operating manuals and safety sheets, view tutorial videos and examine relevant key performance indicators (KPIs). The order management software's asset management module should also include warranty data and any pertinent compliance-related information.
- Work order management: The software should be capable of creating highly detailed work requests and orders, and organizing them in order of priority. Commonly, it will use a ticketing system for orders that allows the facilities management staff to efficiently schedule maintenance jobs.
- Materials and parts: Without these essential components, no maintenance can occur. A quality CMMS or EAM system should provide precise information regarding the quantity and availability of materials and spare parts. Ideally, you should also be able to assign materials or parts to specific assets in your inventory, so that managers and techs are always aware of what's needed to maintain or repair an asset.
- Reporting: The software's dashboard should offer you quick access to comprehensive reports on the overall state of maintenance in your organization. Customization must be an option, as some businesses will want to prioritize different KPIs than others and format reports in various ways.
- Preventive maintenance: By scheduling maintenance and upkeep jobs to occur well before critical or emergency maintenance is necessary, you will keep your equipment in better working condition and extend its life span. Your work order software should allow you to do this, especially for assets that require mandatory, compliance-related maintenance.
- Safety: Working in an asset-intensive industry requires being extra careful. There have to be procedures requiring disable machinery or equipment, preventing employees and workers from being harmed while maintaining equipment. Even though safety is not part of Work Order Software, a strong EAM solution will allow you to manage lockout tagout, work permits and other key safety procedures, by providing easy access to critical information for your workers.
- Mobile access: Even if your techs don't regularly access the work order management module while on the go, it's essential for them to have the option to do so from a mobile device.
Potential maintenance benefits (and challenges to overcome) with work order software
If properly implemented and operated, an effective work order software platform will help your organization realize numerous benefits.
First and foremost, the process of creating, submitting and overseeing a new work order or service request can become much more streamlined through the software's automation. This helps reduce downtime by keeping upkeep and repair operations on an efficient preventive maintenance schedule. In turn, equipment is more likely to last longer and perform better, which can boost production. All of these capabilities can create cost savings and benefit the company's bottom line.
That said, challenges can arise in some circumstances. The initial implementation process can be complex. Also, the tool may need to be operated by someone with reasonable IT experience (ideally, experience that involves work order, CMMS or EAM software). These factors exemplify why it's so important to do research and due diligence when looking for a work order management platform.
Leveraging your work order solution for improved efficiency and safety
As we noted at the outset, facility management without a work order and asset management system simply isn't possible anymore. No technician should be stuck dealing with paper forms or even simple spreadsheets for maintenance orders.
If it's necessary to hire IT staff with specific experience using these solutions, that's a reasonable cost of doing business. So is implementing training that covers the platform's essential functions, as you never know when the team's most experienced members might be absent and others might need to take their place.
But an even better approach to the problem is a more direct one: choosing an EAM from a provider like Dynaway, with a long history of quality. Dynaway EAM is built inside Microsoft Dynamics 365 and has all the critical ERP tools, allowing you to manage work orders while remaining cognizant of the business from a more big-picture perspective. And if seeking ease of use, Dynaway EAM for Business Central is easy to set up and operate "out of the box" without additional IT's assistance.